1. Characteristics and applications of metamaterials
Metamaterials are a new class of materials with artificially engineered microstructures. Their properties primarily depend on the geometric arrangement of their microstructures rather than their intrinsic chemical composition. Through carefully designed periodic or aperiodic structures, metamaterials can exhibit physical characteristics not found or hard to achieve in nature, such as negative refractive index, negative Poisson’s ratio, and negative compressibility. These properties endow them with revolutionary application potential in fields such as mechanics, thermodynamics, and aerospace. The categories and characteristics of mechanical metamaterials are shown in Figure 1 [1].
The performance of metamaterials is realized through a reverse design approach based on the principle of “structure determines function.” For example, auxetic metamaterials (also known as negative Poisson’s ratio metamaterials) achieve such properties through microstructures such as trusses and lattices. Owing to their excellent mechanical performance, they have attracted widespread attention. Numerous researchers have reviewed the design, fabrication, mechanical properties, and potential applications of auxetic metamaterials, and have pointed out current challenges and future directions for intelligent development. Luo et al. reviewed various design methods and advanced manufacturing techniques for auxetic tubes [2] ; Zhang et al. provided a detailed overview of the shape transformation, actuation, sensing, multi-physics responses, and intelligent function integration in the inverse design of auxetic metamaterials [3], as shown in Figure 2 [3] ; Zhang et al. further categorized auxetic materials based on their fundamental topology-property relationships and discussed their deformation mechanisms [4]. Leveraging the inverse design capability of metamaterials, Gabriel et al. applied a sequential framework of topology and shape optimization to design piezoelectric metamaterials with a negative Poisson’s ratio [5]. In addition to auxetic metamaterials, phononic crystal-based metamaterials can also exhibit anomalous wave propagation characteristics through artificially designed topologies or unit cell lattices. Wu et al. summarized recent interdisciplinary developments and current research trends in intelligent metamaterials with electro/magnetic/mechanical coupling, providing timely and comprehensive guidance for future research on actively tunable phononic crystals and metamaterials in practical engineering applications [6].
Due to their superior physical properties, metamaterials have found broad application across multiple domains. In biomedical and electronic information fields, the intelligent potential of auxetic metamaterials has been extended to soft robotics (external), human-machine interaction (peripheral), and medical devices (internal) [3]. They also demonstrate outstanding mechanical performance in protective equipment, sensors, and actuators [4]. In marine engineering, piezoelectric metamaterials are primarily used for sound insulation and energy conversion in underwater equipment [7]. In aerospace applications, a scalable fabrication method has enabled the development of a coral-structured titanium nitride plasmonic metamaterial with omnidirectional absorption exceeding 90% across the visible to long-wave infrared spectrum, demonstrating exceptional reliability under rigorous aerospace-grade testing [8].
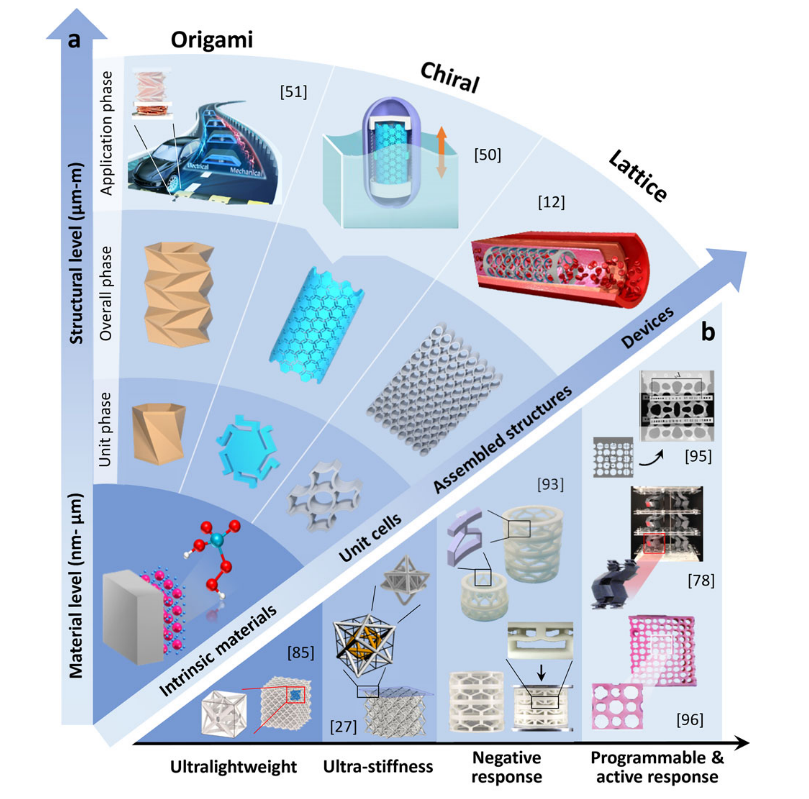
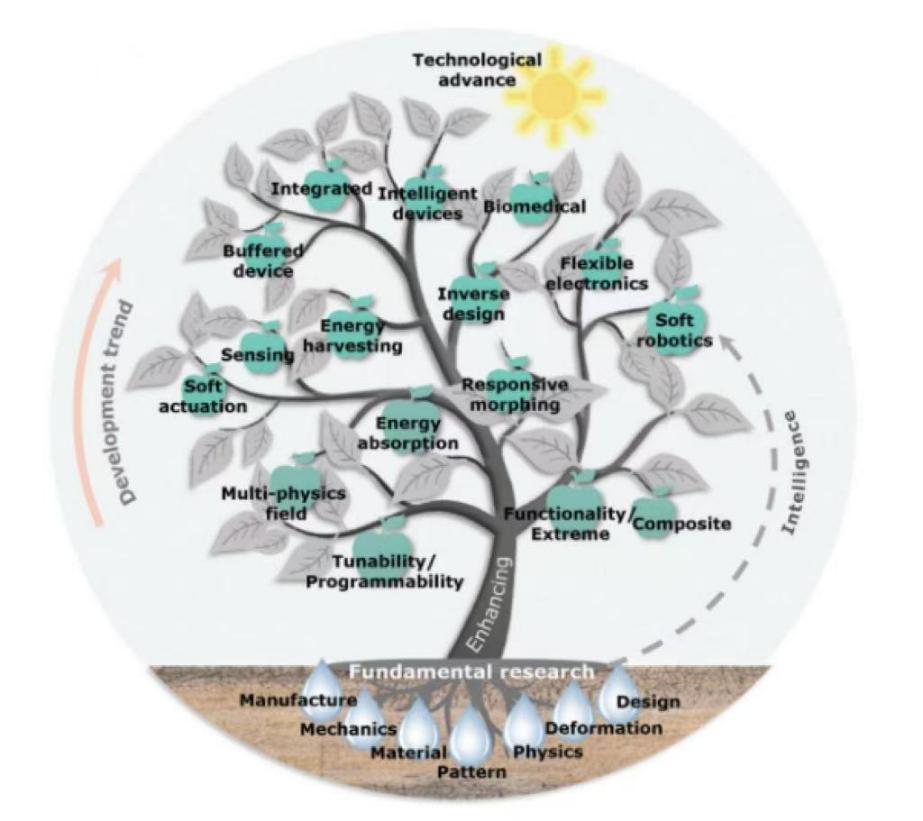
Figure 2: Development tree of auxetic metamaterials from fundamental research to intelligent and integrated applications
2. Structural failure of metamaterials in thermal environments
A thermal environment refers to a comprehensive thermal state formed by the combined effects of physical factors such as temperature distribution and heat transfer within a specific space or system. Its core characteristic lies in influencing the thermal equilibrium of materials or structures through thermodynamic processes. Structural failure under thermal conditions is a critical research topic in the field of mechanical metamaterials. As modern industrial technologies increasingly extend into extreme environments such as aerospace propulsion systems, the stability and reliability of metamaterials under high-temperature conditions have become key constraints on technological advancement.
2.1. Physical mechanisms of structural failure in thermal environments
In high-temperature environments, the microstructures of materials undergo multiple physical and chemical transformations due to heat input. First, atomic vibrations lower the activation energy required for dislocation motion in metallic materials, significantly reducing their yield strength. For example, in nickel-based superalloys, at 950 °C, dislocation motion primarily occurs via climb, and the γ′ phase softens and grows, leading to a marked decline in tensile strength [9]. Second, in composite structures composed of different materials, thermal gradients result in differential thermal expansion, generating interfacial shear stresses that can easily cause delamination failure. Under identical mechanical loads and boundary conditions, elevated temperatures increase the interlaminar shear stress in composite laminated beams [10]. Additionally, phase transformation is another key failure mechanism. For instance, as temperature rises, the zirconium matrix gradually transitions from α-Zr to β-Zr, partially relieving internal stress in the oxide layer and triggering microcrack propagation within the mechanically weaker α-Zr(O) layer [11].
2.2. Typical failure modes of metamaterial structures in thermal environments
The typical failure modes and dynamic processes of structural failure in thermal environments can be broadly categorized into three types: First is creep fracture, which refers to the continuous deformation of a material under prolonged high temperature and stress. For instance, the FCCZ lattice exhibits significantly greater changes in creep rate at 550 °C and 650 °C compared to its base materials under varying stress and temperature conditions [12]. Second is thermal fatigue damage, caused by strain accumulation due to temperature fluctuations. In the case of the FGH96 superalloy, the growth rate of small fatigue cracks increases with rising stress ratios and temperatures [13]. Third is oxidation-corrosion synergistic damage. For example, porous Csf/SiBCN composites, when exposed to 1500 °C for 10 hours, experience a visible collapse of their macroscopic structure [14].
2.3. Research and advances in novel heat-resistant materials
In response to the physical mechanisms and various failure modes of metamaterial structures under thermal environments, the development of new heat-resistant materials has gained momentum and is becoming one of the most promising directions for thermal protection systems. Modern advanced heat-resistant materials mainly fall into three representative systems, each demonstrating excellent thermal properties [15] : (1) Functionally Graded Materials (FGMs) with spatially tunable characteristics. The introduction of gradient structures enhances thermal shock resistance and durability. Compared to single or dual ceramic layer coatings, optimized functionally graded coatings can effectively reduce thermal stresses at crack tips within the coating [16]. (2) Layered porous materials. For instance, the thermal conductivity of A356/316L interpenetrating composites with porosity is significantly lower than the values predicted by simple mixing rules [17]. (3) Next-generation reinforced composites. For example, hafnium carbide-modified flexible carbon nanofibers exhibit a twentyfold increase in thermal conductivity and begin degrading at a higher temperature of 840 °C. Even after exposure to extreme processing at 1850 °C, the fiber structure remains intact [18].
3. Stability and failure analysis of metamaterial structures in extreme environments
The analysis of the stability and failure of metamaterials is widely relevant in engineering domains such as aerospace. In actual engineering applications, metamaterial structures often operate under extreme multi-field coupling environments involving mechanical, thermal, and electromagnetic fields—for instance, the coupled effects of aerodynamic heating and inertial loads during spacecraft reentry [19]. This section comprehensively reviews the stability and failure behaviors of mechanical metamaterials under extreme single-field environments, as well as their mechanical responses and analytical methods under multi-field coupling, aiming to reveal the underlying mechanisms and criteria for stability.
3.1. Stability and failure behaviors under multi-field coupling
First, under mechanical loads, the classical Euler critical load formula describes the buckling threshold of slender rods. This model assumes linear elasticity and small deformations, making it suitable for ideal boundary conditions. However, actual structures frequently experience nonlinear and post-buckling behaviors. Studies have shown that the buckling load of clamped functionally graded plates under asymmetric planar loads is lower than that under axisymmetric loads for the same plate [20]. Second, under thermal effects, when thermal expansion is constrained, thermal stress arises. Research indicates that when steel–steel composite metal foams exceed 600 °C, their strength deteriorates rapidly due to thermal softening, oxidation, and plastic buckling; at 800 °C, their structural integrity is severely compromised [21]. Third, under electromagnetic fields, ferromagnetic and piezoelectric materials exhibit magnetostriction and electrostriction effects, respectively, leading to strain and the generation of additional stress fields. For example, in magnetostrictive composites containing 70% volume fraction of Terfenol-D powder, vertically polarized samples achieved the highest magnetostriction value, with a strain of 720 ppm under a prestress of 7 MPa [22]. Wu et al. considered the nonlinear behavior of piezoelectric materials under strong electric fields and established a cable dynamic model incorporating von Kármán-type nonlinearity and sag effects. The results showed that strain predictions without considering strong electric fields were 57.52% lower than finite element calculations, thereby validating the model’s accuracy [23].
3.2. Mechanical responses and analytical methods under multi-field coupling
In recent years, as composite materials increasingly encounter coupled loadings such as thermo-electromagnetic or thermo-electro-mechanical loads, investigations into their mechanical responses and analytical approaches under these conditions have intensified. Kim et al. developed a first-order shear deformation theory (FSDT) model for laminated composite plates under combined electromagnetic and thermal fields. The coupled motion equations were based on electromagnetic and heat conduction equations, and they also analyzed the vibration responses of the plates in relation to magnetic field strength, thermal loads, and electrical conductivity [24]. Zhu et al. formulated nonlinear large-deflection control equations for magneto-electro-elastic (MEE) cylindrical shells based on higher-order shear deformation theory, examining the effects of multi-field coupled loads on post-buckling behavior [25]. Guo et al. proposed a nonlinear model for piezoelectric laminated composite (PLC) structures that incorporates both geometric and material nonlinearities to accurately predict the static and dynamic responses under thermo-electro-mechanical loading [26]. Zhang et al. developed a nonlinear analysis model that comprehensively accounts for geometric and piezoelectric nonlinearities as well as the temperature dependence of piezoelectric parameters, enabling accurate predictions of the nonlinear behaviors of functionally graded piezoelectric plates under large thermo-electro-mechanical loads [27], and the nonlinear frequencies of graphene-reinforced functionally graded porous piezoelectric plates under such conditions [28].
4. Conclusion
The performance of mechanical metamaterials is primarily realized through inverse design and has found broad applications in fields such as biomedicine, electronic information, marine engineering, and aerospace. The physical mechanisms of failure for metamaterials in thermal environments mainly include reduced activation energy for dislocation motion, the generation of interfacial shear stress, and phase transformation. Typical failure modes encompass creep rupture, thermal fatigue damage, and synergistic oxidation-corrosion damage. Research into novel heat-resistant materials—such as functionally graded materials, porous materials, and reinforced composites—is steadily advancing. The stability and failure of metamaterials under extreme single-field environments can be analyzed from the perspectives of mechanical, thermal, and electromagnetic loading. Their mechanical responses under multi-field coupling are primarily addressed by establishing specific analytical models or equations.
References
[1]. Jiao, P. , Mueller, J. , Raney, J. R. , Zheng, X. , & Alavi, A. H. (2023). Mechanical metamaterials and beyond. Nature communications, 14(1), 6004.
[2]. Luo, C. , Han, C. Z. , Zhang, X. Y. , Zhang, X. G. , & Ren, X. (2021). Design, manufacturing and applications of auxetic tubular structures: A review. Thin-Walled Structures, 163, 107682.
[3]. Zhang, Y. , Jiang, W. Z. , Jiang, W. , Zhang, X. Y. , Dong, J. , . . . & Ren, X. (2025). Recent Advances of Auxetic Metamaterials in Smart Materials and Structural Systems. Advanced Functional Materials, 2421746.
[4]. Zhang, L. , Yan, S. , Liu, W. , Liu, Y. , Cai, W. , Zhang, Z. , & Zhou, J. (2025). Mechanical metamaterials with negative Poisson’s ratio: A review. Engineering Structures, 329, 119838.
[5]. Stankiewicz, G. , Dev, C. , Weichelt, M. , Fey, T. , & Steinmann, P. (2024). Towards advanced piezoelectric metamaterial design via combined topology and shape optimization. Structural and Multidisciplinary Optimization, 67(2), 26.
[6]. Wu, B. , Jiang, W. , Jiang, J. , Zhao, Z. , Tang, Y. , Zhou, W. , & Chen, W. (2024). Wave manipulation in intelligent metamaterials: recent progress and prospects. Advanced Functional Materials, 34(29), 2316745.
[7]. Zhao, J. , Hu, N. , Wu, J. , Li, W. , Zhu, Z. , Wang, M. , . . . & Dai, H. (2022). A review of piezoelectric metamaterials for underwater equipment. Frontiers in Physics, 10, 1068838.
[8]. Li, Y. , Huang, Z. , Xu, Y. , Zhang, H. , Wang, Q. , Qiao, H. , . . . & Cui, K. (2022). Scalable‐manufactured plasmonic metamaterial with omnidirectional absorption bandwidth across visible to far‐infrared. Advanced Functional Materials, 32(46), 2207239.
[9]. Jiang, Y. , Zou, T. , Liu, M. , Wang, Q. , Pei, Y. , Zhang, H. , . . . & Wang, Q. (2024). Tensile Deformation Behaviors and Microstructure Evolution Under Various Temperatures for MAR‐M247 Nickel‐Based Superalloy. Advanced Engineering Materials, 26(12), 2302056.
[10]. Murugesan, N. , & Rajamohan, V. (2015). Investigation on interlaminar shear stresses in laminated composite beam under thermal and mechanical loading. Steel Compos Struct, 18(3), 583-601.
[11]. Sun, H. , Zhang, Y. , Zhu, X. , Xu, C. , Sun, C. , & Luan, B. (2023). Study of oxidation behavior and associated microstructure evolution of Zircaloy-4 exposed to high temperature pure steam. Vacuum, 211, 111892.
[12]. Fitzgerald, K. M. , Berfield, T. A. , Torbati‐Sarraf, H. , & Pataky, G. J. (2023). Compressive creep buckling of single cell metamaterial at elevated temperatures. Fatigue & Fracture of Engineering Materials & Structures, 46(2), 366-378.
[13]. Liu, A. , Zhang, Y. T. , Wang, X. S. , Xu, W. , Zhang, Y. , & He, Y. H. (2023). Evaluation of the influences of the stress ratio, temperatures, and local microstructure on small fatigue crack propagation behavior of the FGH96 superalloy. International Journal of Fatigue, 171, 107573.
[14]. Dou, W. , Li, D. , Wang, B. , Yang, Z. , Jia, D. , Riedel, R. , & Zhou, Y. (2024). Microstructural evolution and oxide layer structure of Csf/SiBCN composites during oxidation at 1500℃. Journal of the European Ceramic Society, 44(7), 4452-4464.
[15]. Li, S. P. , Zuo, G. Q. , Zhang, C. L. , Erasmo, C. , & Chen, W. Q. (2025). Recent progress in thermal structures: Materials, structures, and analyses. Composite Structures, 119037.
[16]. Wang, Y. , Wang, C. , You, Y. , Cheng, W. , Dong, M. , Zhu, Z. , . . . & Wang, Y. (2023). Thermal stress analysis of optimized functionally graded coatings during crack propagation based on finite element simulation. Surface and Coatings Technology, 463, 129535.
[17]. Moustafa, A. R. , Dinwiddie, R. B. , Pawlowski, A. E. , Splitter, D. A. , Shyam, A. , & Cordero, Z. C. (2018). Mesostructure and porosity effects on the thermal conductivity of additively manufactured interpenetrating phase composites. Additive Manufacturing, 22, 223-229.
[18]. Nisar, A. , Lou, L. , Boesl, B. , & Agarwal, A. (2023). Enhanced flexibility and thermal conductivity of HfC decorated carbon nanofiber mats. Carbon, 205, 573-582.
[19]. Zhang, Y. , Guo, X. , Wu, Y. , Zhang, Y. , Zhang, H. , & Lü, C. (2024). Vibration control of membrane structures by piezoelectric actuators considering piezoelectric nonlinearity under strong electric fields. Engineering Structures, 315, 118413.
[20]. Fallah, F. , Vahidipoor, M. K. , & Nosier, A. (2015). Post-buckling behavior of functionally graded circular plates under asymmetric transverse and in-plane loadings. Composite Structures, 125, 477-488.
[21]. Chacko, Z. , Yeboah, N. A. , & Rabiei, A. (2025). A Study on Thermal Expansion and Thermomechanical Behavior of Composite Metal Foams. Advanced Engineering Materials, 2402871.
[22]. Kaleta, J. , Lewandowski, D. , & Mech, R. (2015). Magnetostriction of field-structural composite with Terfenol-D particles. Archives of Civil and Mechanical Engineering, 15(4), 897-902.
[23]. Wu, Y. , Zhang, Y. , Guo, X. , Zhang, Y. , Zhang, H. , & Lü, C. (2024). Active control of cable vibration using piezoelectric actuators considering strong electric field nonlinearity. Journal of Vibration Engineering & Technologies, 1-13.
[24]. Kim, S. K. , Choi, J. , Park, S. , & Song, O. (2015). Vibration and stability of laminated composite plates subjected to a combined electromagnetic and thermal field. Journal of Vibration and Control, 21(12), 2325-2339.
[25]. Zhu, S. , Sun, J. , Tong, Z. , Li, Q. , Zhou, Z. , & Xu, X. (2021). Post-buckling analysis of magneto-electro-elastic composite cylindrical shells subjected to multi-field coupled loadings. Composite Structures, 270, 114061.
[26]. Guo, X. , Zhang, Y. , Wu, Y. , Zhang, Y. , Zhang, H. , & Lü, C. (2025). Nonlinear thermo-electro-mechanical analysis of piezoelectric laminated composite beams considering strong electric field. Engineering Structures, 325, 119457.
[27]. Zhang, Y. , Guo, X. , Wu, Y. , Zhang, Y. , Zhang, H. , & Lü, C. (2024). Nonlinear thermo-electro-mechanical responses and active control of functionally graded piezoelectric plates subjected to strong electric fields. Thin-Walled Structures, 205, 112375.
[28]. Zhang, Y. , Guo, X. , Ni, Z. , Zhang, Y. , Zhang, H. , Lü, C. , & Yang, J. (2025). Nonlinear frequency analysis of piezoelectric functionally graded porous plates reinforced by graphene platelets under thermo-electro-mechanical loads. Mechanics of Advanced Materials and Structures, 1-17.
Cite this article
Liu,J. (2025). A review of the applications of mechanical metamaterials in extreme environments. Advances in Engineering Innovation,16(6),112-116.
Data availability
The datasets used and/or analyzed during the current study will be available from the authors upon reasonable request.
Disclaimer/Publisher's Note
The statements, opinions and data contained in all publications are solely those of the individual author(s) and contributor(s) and not of EWA Publishing and/or the editor(s). EWA Publishing and/or the editor(s) disclaim responsibility for any injury to people or property resulting from any ideas, methods, instructions or products referred to in the content.
About volume
Journal:Advances in Engineering Innovation
© 2024 by the author(s). Licensee EWA Publishing, Oxford, UK. This article is an open access article distributed under the terms and
conditions of the Creative Commons Attribution (CC BY) license. Authors who
publish this series agree to the following terms:
1. Authors retain copyright and grant the series right of first publication with the work simultaneously licensed under a Creative Commons
Attribution License that allows others to share the work with an acknowledgment of the work's authorship and initial publication in this
series.
2. Authors are able to enter into separate, additional contractual arrangements for the non-exclusive distribution of the series's published
version of the work (e.g., post it to an institutional repository or publish it in a book), with an acknowledgment of its initial
publication in this series.
3. Authors are permitted and encouraged to post their work online (e.g., in institutional repositories or on their website) prior to and
during the submission process, as it can lead to productive exchanges, as well as earlier and greater citation of published work (See
Open access policy for details).
References
[1]. Jiao, P. , Mueller, J. , Raney, J. R. , Zheng, X. , & Alavi, A. H. (2023). Mechanical metamaterials and beyond. Nature communications, 14(1), 6004.
[2]. Luo, C. , Han, C. Z. , Zhang, X. Y. , Zhang, X. G. , & Ren, X. (2021). Design, manufacturing and applications of auxetic tubular structures: A review. Thin-Walled Structures, 163, 107682.
[3]. Zhang, Y. , Jiang, W. Z. , Jiang, W. , Zhang, X. Y. , Dong, J. , . . . & Ren, X. (2025). Recent Advances of Auxetic Metamaterials in Smart Materials and Structural Systems. Advanced Functional Materials, 2421746.
[4]. Zhang, L. , Yan, S. , Liu, W. , Liu, Y. , Cai, W. , Zhang, Z. , & Zhou, J. (2025). Mechanical metamaterials with negative Poisson’s ratio: A review. Engineering Structures, 329, 119838.
[5]. Stankiewicz, G. , Dev, C. , Weichelt, M. , Fey, T. , & Steinmann, P. (2024). Towards advanced piezoelectric metamaterial design via combined topology and shape optimization. Structural and Multidisciplinary Optimization, 67(2), 26.
[6]. Wu, B. , Jiang, W. , Jiang, J. , Zhao, Z. , Tang, Y. , Zhou, W. , & Chen, W. (2024). Wave manipulation in intelligent metamaterials: recent progress and prospects. Advanced Functional Materials, 34(29), 2316745.
[7]. Zhao, J. , Hu, N. , Wu, J. , Li, W. , Zhu, Z. , Wang, M. , . . . & Dai, H. (2022). A review of piezoelectric metamaterials for underwater equipment. Frontiers in Physics, 10, 1068838.
[8]. Li, Y. , Huang, Z. , Xu, Y. , Zhang, H. , Wang, Q. , Qiao, H. , . . . & Cui, K. (2022). Scalable‐manufactured plasmonic metamaterial with omnidirectional absorption bandwidth across visible to far‐infrared. Advanced Functional Materials, 32(46), 2207239.
[9]. Jiang, Y. , Zou, T. , Liu, M. , Wang, Q. , Pei, Y. , Zhang, H. , . . . & Wang, Q. (2024). Tensile Deformation Behaviors and Microstructure Evolution Under Various Temperatures for MAR‐M247 Nickel‐Based Superalloy. Advanced Engineering Materials, 26(12), 2302056.
[10]. Murugesan, N. , & Rajamohan, V. (2015). Investigation on interlaminar shear stresses in laminated composite beam under thermal and mechanical loading. Steel Compos Struct, 18(3), 583-601.
[11]. Sun, H. , Zhang, Y. , Zhu, X. , Xu, C. , Sun, C. , & Luan, B. (2023). Study of oxidation behavior and associated microstructure evolution of Zircaloy-4 exposed to high temperature pure steam. Vacuum, 211, 111892.
[12]. Fitzgerald, K. M. , Berfield, T. A. , Torbati‐Sarraf, H. , & Pataky, G. J. (2023). Compressive creep buckling of single cell metamaterial at elevated temperatures. Fatigue & Fracture of Engineering Materials & Structures, 46(2), 366-378.
[13]. Liu, A. , Zhang, Y. T. , Wang, X. S. , Xu, W. , Zhang, Y. , & He, Y. H. (2023). Evaluation of the influences of the stress ratio, temperatures, and local microstructure on small fatigue crack propagation behavior of the FGH96 superalloy. International Journal of Fatigue, 171, 107573.
[14]. Dou, W. , Li, D. , Wang, B. , Yang, Z. , Jia, D. , Riedel, R. , & Zhou, Y. (2024). Microstructural evolution and oxide layer structure of Csf/SiBCN composites during oxidation at 1500℃. Journal of the European Ceramic Society, 44(7), 4452-4464.
[15]. Li, S. P. , Zuo, G. Q. , Zhang, C. L. , Erasmo, C. , & Chen, W. Q. (2025). Recent progress in thermal structures: Materials, structures, and analyses. Composite Structures, 119037.
[16]. Wang, Y. , Wang, C. , You, Y. , Cheng, W. , Dong, M. , Zhu, Z. , . . . & Wang, Y. (2023). Thermal stress analysis of optimized functionally graded coatings during crack propagation based on finite element simulation. Surface and Coatings Technology, 463, 129535.
[17]. Moustafa, A. R. , Dinwiddie, R. B. , Pawlowski, A. E. , Splitter, D. A. , Shyam, A. , & Cordero, Z. C. (2018). Mesostructure and porosity effects on the thermal conductivity of additively manufactured interpenetrating phase composites. Additive Manufacturing, 22, 223-229.
[18]. Nisar, A. , Lou, L. , Boesl, B. , & Agarwal, A. (2023). Enhanced flexibility and thermal conductivity of HfC decorated carbon nanofiber mats. Carbon, 205, 573-582.
[19]. Zhang, Y. , Guo, X. , Wu, Y. , Zhang, Y. , Zhang, H. , & Lü, C. (2024). Vibration control of membrane structures by piezoelectric actuators considering piezoelectric nonlinearity under strong electric fields. Engineering Structures, 315, 118413.
[20]. Fallah, F. , Vahidipoor, M. K. , & Nosier, A. (2015). Post-buckling behavior of functionally graded circular plates under asymmetric transverse and in-plane loadings. Composite Structures, 125, 477-488.
[21]. Chacko, Z. , Yeboah, N. A. , & Rabiei, A. (2025). A Study on Thermal Expansion and Thermomechanical Behavior of Composite Metal Foams. Advanced Engineering Materials, 2402871.
[22]. Kaleta, J. , Lewandowski, D. , & Mech, R. (2015). Magnetostriction of field-structural composite with Terfenol-D particles. Archives of Civil and Mechanical Engineering, 15(4), 897-902.
[23]. Wu, Y. , Zhang, Y. , Guo, X. , Zhang, Y. , Zhang, H. , & Lü, C. (2024). Active control of cable vibration using piezoelectric actuators considering strong electric field nonlinearity. Journal of Vibration Engineering & Technologies, 1-13.
[24]. Kim, S. K. , Choi, J. , Park, S. , & Song, O. (2015). Vibration and stability of laminated composite plates subjected to a combined electromagnetic and thermal field. Journal of Vibration and Control, 21(12), 2325-2339.
[25]. Zhu, S. , Sun, J. , Tong, Z. , Li, Q. , Zhou, Z. , & Xu, X. (2021). Post-buckling analysis of magneto-electro-elastic composite cylindrical shells subjected to multi-field coupled loadings. Composite Structures, 270, 114061.
[26]. Guo, X. , Zhang, Y. , Wu, Y. , Zhang, Y. , Zhang, H. , & Lü, C. (2025). Nonlinear thermo-electro-mechanical analysis of piezoelectric laminated composite beams considering strong electric field. Engineering Structures, 325, 119457.
[27]. Zhang, Y. , Guo, X. , Wu, Y. , Zhang, Y. , Zhang, H. , & Lü, C. (2024). Nonlinear thermo-electro-mechanical responses and active control of functionally graded piezoelectric plates subjected to strong electric fields. Thin-Walled Structures, 205, 112375.
[28]. Zhang, Y. , Guo, X. , Ni, Z. , Zhang, Y. , Zhang, H. , Lü, C. , & Yang, J. (2025). Nonlinear frequency analysis of piezoelectric functionally graded porous plates reinforced by graphene platelets under thermo-electro-mechanical loads. Mechanics of Advanced Materials and Structures, 1-17.