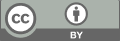
Research on metal image defect detection based on convolutional neural network, random forest model and support vector machine model
- 1 Henan University of Economics and Law
* Author to whom correspondence should be addressed.
Abstract
Metal image defect detection is a very important task, which can help manufacturers to detect defects in metal products in time during the production process, so as to improve product quality and production efficiency. This paper presents a private dataset containing images of six different types of metal surface defects, including scratches, pits, indentations, bubbles, oil stains, and aluminum surface defects. The dataset contains 1800 images, 300 images for each defect type, each with a size of 200x200 pixels. The dataset is divided into training, validation and test sets in the ratio of 6:2:2. By using Support Vector Machine Model, Random Forest Model and Convolutional Neural Network Model for prediction, we obtained the following results: the Support Vector Machine Model has the best prediction ability with 89% accuracy; the Random Forest Model has 69% accuracy; and the Convolutional Neural Network Model has poor prediction ability with 26% accuracy. From these results, it can be seen that the support vector machine model is one of the most suitable models for defect detection in metal images. This model can effectively identify various defects on metal surfaces, thus helping manufacturers to better control the quality of their products. In comparison, the predictive power of the Random Forest model is weak, but it can still be used for some simple metal image defect detection tasks. The convolutional neural network model has the worst predictive ability, but it is widely used in other fields, such as image recognition and speech recognition. In conclusion, metal image defect detection is a very important task, which can help manufacturers find the defects of metal products in the production process in time, so as to improve product quality and production efficiency. In practical applications, we can choose different algorithms and models to realize metal image defect detection in order to get the best results.
Keywords
CNN, Machine learning algorithms, SVM
[1]. Zhao L ,Zheng Y ,Peng T , et al.Metal Surface Defect Detection Based on a Transformer with Multi-Scale Mask Feature Fusion[J].Sensors,2023,23(23):
[2]. Yiming G ,Yiyang S ,Jie W , et al.Superior Electromechanical Compatibility in Lead-Free Piezoceramics with Mobile Transition-Metal Defects.[J].ACS applied materials interfaces,2023,
[3]. Meng S ,Lijian Y ,Songwei G , et al.Metal Surface Defect Detection Method Based on TE01 Mode Microwave[J].Sensors,2022,22(13):4848-4848.
[4]. Ihor K ,Pavlo M ,Janette B , et al.Research of U-Net-Based CNN Architectures for Metal Surface Defect Detection[J].Machines,2022,10(5):327-327.
[5]. Kun W ,Zixuan T ,Tengyue Z .Metal Defect Detection Based on Yolov5[J].Journal of Physics: Conference Series,2022,2218(1):
[6]. V. V P ,S. E D .Testing for Defects in Pulsed Magnetic Field Transmitted Through Metal[J].Russian Journal of Nondestructive Testing,2022,57(10):856-864.
[7]. Yiming X ,Kai Z ,Li W .Metal Surface Defect Detection Using Modified YOLO[J].Algorithms,2021,14(9):257-257.
[8]. I N G ,A N K ,A A B , et al.Research of the occurrence and development of metal defects in sulfide stress cracking inducing environment[J].IOP Conference Series: Materials Science and Engineering,2021,1129(1):
[9]. Chowdary D S ,Sudhakar M . Multi-objective Floorplanning optimization engaging dynamic programming for system on chip[J]. Microelectronics Journal,2023,140.
[10]. JinPei D ,WenHua C ,HsienChang K , et al.Efficient small toxic gaseous molecule scavengers in metal‐defective graphene: A density functional analysis[J].Journal of the Chinese Chemical Society,2021,68(3):517-521.
Cite this article
Tao,Y. (2024). Research on metal image defect detection based on convolutional neural network, random forest model and support vector machine model. Applied and Computational Engineering,45,312-318.
Data availability
The datasets used and/or analyzed during the current study will be available from the authors upon reasonable request.
Disclaimer/Publisher's Note
The statements, opinions and data contained in all publications are solely those of the individual author(s) and contributor(s) and not of EWA Publishing and/or the editor(s). EWA Publishing and/or the editor(s) disclaim responsibility for any injury to people or property resulting from any ideas, methods, instructions or products referred to in the content.
About volume
Volume title: Proceedings of the 4th International Conference on Signal Processing and Machine Learning
© 2024 by the author(s). Licensee EWA Publishing, Oxford, UK. This article is an open access article distributed under the terms and
conditions of the Creative Commons Attribution (CC BY) license. Authors who
publish this series agree to the following terms:
1. Authors retain copyright and grant the series right of first publication with the work simultaneously licensed under a Creative Commons
Attribution License that allows others to share the work with an acknowledgment of the work's authorship and initial publication in this
series.
2. Authors are able to enter into separate, additional contractual arrangements for the non-exclusive distribution of the series's published
version of the work (e.g., post it to an institutional repository or publish it in a book), with an acknowledgment of its initial
publication in this series.
3. Authors are permitted and encouraged to post their work online (e.g., in institutional repositories or on their website) prior to and
during the submission process, as it can lead to productive exchanges, as well as earlier and greater citation of published work (See
Open access policy for details).