1. Introduction
Traditional site building projects involve the transportation of goods, tradespeople, and workers to the construction site. This technique encompasses a significant section of the architectural, engineering, and construction (AEC) business [1]. With the advent of industrialization and information technology, off-site construction has increasingly supplanted on-site construction in recent years. Off-site construction refers to the method of producing and pre-assembling building pieces, components, or modules before they are installed on-site [2]. Nevertheless, this innovative building method may still have inherent hazards during the stages of manufacture, transportation, assembly, and other related processes.
Risks encompass both detrimental and beneficial characteristics. Managers strive to prevent or reduce adverse risks (threats) while capitalizing on or enhancing favorable risks (opportunities) [3]. An issue in risk management is the dynamic nature of risks, which can fluctuate over time. Failure to minimize or mitigate project risks will have a detrimental effect on the project. The project team is accountable for mitigating risk by employing suitable tools. Ameyaw et al. emphasize the importance of identifying risks by considering three fundamental aspects of project scope: time, money, and quality [4], as seen in figure 1. Nevertheless, conventional MiCRM systems require manual effort and are time-consuming. Researchers have been compelled to seek other approaches due to the inefficiency and high expense of existing ones. Utilizing Building Information Modeling (BIM) in MiCRM has emerged as a recent phenomenon, where project teams employ BIM for the purpose of information management and collaboration, enabling comprehensive monitoring of project execution and goal setting. Simultaneously, the integration of certain cutting-edge digital technologies with BIM can address its shortcomings and effectively enhance the performance of MiCRM. Nevertheless, because of the gravity of BIM and its impact on various aspects, BIM-based MiCRM has faced certain obstacles.
This research employs the literature review method to examine the significant factors driving the adoption of Building Information Modeling (BIM) in Mobile Customer Relationship Management (MiCRM). Additionally, it evaluates the obstacles encountered in implementing BIM-based MiCRM. The importance of this study is in the utilization of BIM technology and the modular integrated construction concept to enhance the effectiveness of risk management in the construction sector and diminish the financial burden associated with construction projects. It serves as a guide for the future development of construction projects.
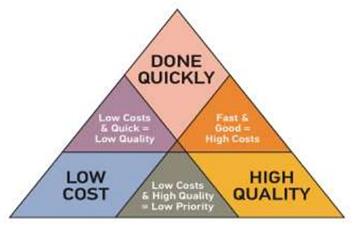
Figure 1. Time, Cost and Quality [4]
2. Implement MiCRM through BIM
2.1. MiCRM is used separately by BIM
During the manufacturing stage, manufacturers and suppliers have the ability to utilize advanced BIM simulation models in the MiC. This technology has the capability to incorporate a significant amount of data, as noted by Drawbotics [5]. Figure 2 illustrates many aspects of project management, including 3D visualization, 4D time planning, 5D cost estimation, 6D operational planning, 7D sustainability, 8D safety, and other related factors. During the module production process, a better understanding of site information and more rational scheduling of different facilities can lead to cost savings, while guaranteeing sustainability and safety. This, in turn, reduces manufacturing errors and mitigates manufacturing hazards.
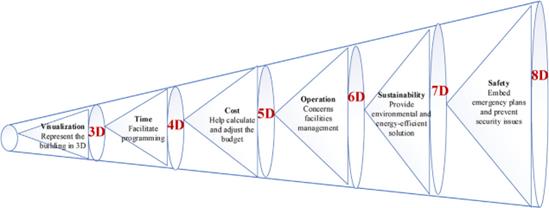
Figure 2. BIM dimensions [5]
During the logistics phase, Building Information Modeling (BIM) provides a comprehensive visualization of the whole building process, allowing project managers to efficiently plan and optimize logistics workflows. By generating intricate 3D representations of modular components and integrating them with logistical information such as material amounts, delivery timetables, and storage needs. The conflict detection features of BIM assist in identifying potential conflicts among modular pieces, equipment, and field logistics. This allows for early adjustments and helps reduce delays and bottlenecks. Furthermore, BIM facilitates instantaneous collaboration among stakeholders, enabling smooth communication and the exchange of information during the logistics stage. By optimizing resource allocation, reducing errors, enhancing coordination, and improving the efficiency and productivity of the construction process, significant improvements can be achieved.
During the building and assembly phase, Qihua Tong advocated the use of Building Information Modeling (BIM) for risk management in subway construction schedules. Specifically, a 4D simulation model of BIM is employed to simulate the construction timetable [6]. Through the utilization of Building Information Modeling (BIM), construction professionals are able to actively monitor and manage construction resources, as well as determine the availability of different materials during the development process. This leads to a reduction in potential risks that may arise during construction. Optimizing construction management decision-making processes can help minimize time requirements and assure optimal construction outcomes. Simultaneously, by utilizing the 4D simulation model of Building Information Modeling (BIM), the manager can systematically organize the building plan in accordance with the method depicted in Figure 3. This ensures the smooth progression of all stages and reduces the overall duration of the project.
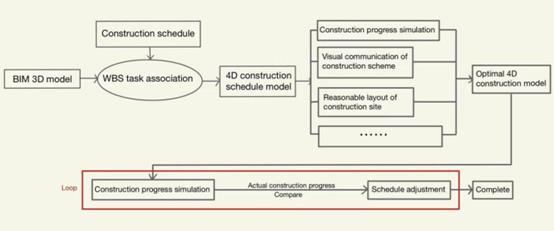
Figure 3. Progress management process based on BIM technology [6]
In addition, Yang Zou et al. state that BIM can enhance collaboration and communication in the context of risk management [7]. Within MiC projects, whether in manufacturing, logistics, or assembly stages, a multitude of individuals from many disciplines are consistently involved. These diverse knowledge systems often result in differing perspectives on the same topic, which in turn leads to cooperation risks. Nevertheless, the cross-disciplinary coordination skills of BIM can be harnessed to establish a vertical integration of information flow, thereby facilitating diverse communication contexts.
2.2. MiCRM works with BIM and related digital technologies
2.2.1. BIM and SST. BIM is a centralized platform that facilitates the management of logistics and product data. It offers project teams significant insights into the design, fabrication, and installation of modular components. Simultaneously, Speech-to-Text (STT) enhances Building Information Modeling (BIM) by offering up-to-the-minute geographical information for precise monitoring and supervision of construction operations and site circumstances.
STT utilizes sensors and IoT devices to collect a diverse variety of data, such as worker mobility, equipment usage, material transportation, and environmental conditions. The extensive dataset is subsequently incorporated into the BIM model, allowing project managers to obtain a comprehensive perspective of the construction site and detect possible hazards or inefficiencies. For instance, in cases where there is a delay in material delivery or personnel are operating in dangerous zones, the integration of Building Information Modeling (BIM) and Smart Tracking Technology (STT) can promptly generate alerts or inform project managers in real time. By utilizing this information, project managers can promptly address developing difficulties, execute corrective measures, and enhance project workflows to guarantee adherence to safety rules and project timeframes. Furthermore, the combination of BIM (Building Information Modeling) with STT (Schedule Tracking Tool) allows for the use of predictive analytics and proactive risk mitigation techniques. Through the examination of past data and present patterns, project teams can predict probable issues in advance, thereby reducing the likelihood of accidents, delays, or exceeding budget limits.
2.2.2. BIM and 3D-MCCT. One significant benefit of 3D-MCCT is its capacity to streamline the inspection and assessment procedure of modular components. By implementing automation for these duties, project teams can greatly diminish the amount of time and effort needed for manual inspections, while simultaneously enhancing the precision and dependability of the gathered data.
The use of 3D-MCCT and BIM platform enhances the efficiency and efficacy of the construction process. By integrating intricate 3D models of modular components with BIM’s extensive data management capabilities, project teams can effortlessly synchronize and cooperate across several fields. This integration facilitates enhanced communication, synchronization, and decision-making, ultimately resulting in enhanced project outcomes and heightened productivity. Furthermore, the pre-conflict detection capabilities of 3D-MCCT aid in minimizing errors and the need for rework in the construction process. By preemptively detecting potential conflicts and clashes among module components before to the commencement of construction, project teams can proactively address these concerns, thereby minimizing the likelihood of schedule delays and cost overruns. This proactive strategy not only enhances the effectiveness of the project, but also optimizes the consumption of resources and reduces waste during the construction process.
3. Challenge analysis
First, BIM, as the cornerstone of MiC, relies heavily on the experience and knowledge of people [8]. While BIM provides a powerful platform for collaborative design and project management, its effectiveness depends on an individual’s proficiency with its capabilities. Inadequate training or lack of understanding of BIM tools can hinder their seamless integration with MiC projects, resulting in errors, delays and increased risk.
Second, the integration of BIM with other digital technologies is still in its infancy, foreshadowing potential uncertainty and complexity in construction projects. The interoperability of different software systems and the merging of data from different sources present significant challenges in ensuring the accuracy and reliability of project information. In addition, the lack of past use cases and practical experience has compounded the complexity of risk management efforts. This initial phase of integration highlights the urgent need for an integrated strategy to address interoperability issues, simplify data exchange protocols, and foster expertise among stakeholders to effectively navigate the evolving landscape of BIM-based construction projects.
Third, the collaborative nature of construction projects requires cohesive teamwork, but the decentralized structure of MiC introduces complexity in risk identification and management. Unlike traditional construction methods, where risks are more concentrated and easier to mitigate, MiC projects involve many modules that must be managed and evaluated separately. From design flaws to logistical challenges, each module can bring its own set of risks that require meticulous coordination and communication among stakeholders. This decentralized approach to risk management requires greater vigilance to prevent risks from being overlooked or mismanaged, as they have the potential to be linked throughout the project if left unaddressed. The need for cross-functional collaboration also adds another layer of complexity, as different stakeholders must work together to effectively identify, assess, and mitigate risks. In addition, because the project is done by a team, any common risks are identified and dealt with separately, and the corresponding information is sometimes overlooked or forgotten during the work and handover [9].
Fourth, the modular nature of MiC projects presents unique challenges in terms of knowledge diversity. Each module operates as a separate entity, requiring multidisciplinary expertise for integrated analysis and decision making. From structural integrity to mechanical systems, stakeholders must have extensive knowledge to effectively navigate complex MiC projects. Failure to combine disparate expertise can lead to the neglect of key elements, thereby compromising the overall success and safety of the construction effort. And the integration of individual modules into the overall project requires careful consideration of compatibility and interoperability, which further emphasizes the need for interdisciplinary collaboration and expertise.
Fifth, the risk management challenges of BIM-based modular integrated construction are exacerbated by the unique socio-economic and infrastructure environments of middle-income countries. In these countries, projects often face additional obstacles, such as inadequate infrastructure, unstable political environments, and varying levels of regulatory compliance. These factors further complicate risk prediction and mitigation efforts as they can significantly affect project timelines, budgets and overall viability. And the lack of standardized protocols and guidelines for implementing BIM and related digital technologies in these regions adds another layer of challenge. Without a clear framework for interoperability and data exchange, stakeholders may struggle to effectively leverage BIM tools for risk management, leading to inefficiencies and increased vulnerabilities. In addition, rapid urbanization and population growth in many middle-income countries are putting enormous pressure on construction projects to meet rising demand, further amplifying the risks associated with resource shortages, environmental degradation, and social inequality. In this context, addressing the challenges of BIM-based risk management in middle-income countries requires a targeted approach that takes into account socio-economic, political and environmental factors specific to middle-income countries. This will require collaboration not only among construction industry stakeholders, but also with government agencies, regulators and local communities to develop comprehensive risk management strategies that promote sustainability and resilience in the face of uncertainty.
4. Conclusions
By effectively merging BIM with MiCRM, projects can attain unparalleled levels of efficiency, precision, and profitability. This collaboration allows for immediate tracking and examination of project information, improving the process of making decisions and actively reducing potential risks. BIM application streamlines the production, logistics, construction, and assembly of project components, while also enhancing collaboration among stakeholders throughout the project lifecycle. The collaborative environment fosters enhanced communication, collaboration, and dispute resolution, ultimately resulting in more seamless project implementation and superior outcomes. Furthermore, by utilizing the integration of BIM with pertinent digital technologies, it is possible to enhance simulation and visualization capabilities to a more sophisticated level. This enables stakeholders to anticipate potential risks, simulate different scenarios, and implement efficient measures to mitigate them, thereby ensuring the success of the project.
Nevertheless, it is crucial to acknowledge the difficulties associated with implementing Building Information Modeling (BIM) in MiCRM. These challenges include the heavy reliance on human expertise and understanding for BIM technology, the early stages of integrating BIM with other related technologies, the intricate nature of risk management in MiC projects, and the differing degrees of technical infrastructure found in middle-income nations. To tackle these difficulties, a comprehensive strategy is needed, which include technical advancements, changes in regulations, and activities to enhance capabilities.
Further study should prioritize the investigation of the potential synergies between Building Information Modeling (BIM) and cutting-edge technologies like artificial intelligence, machine learning, and the Internet of Things (IoT) in order to advance the practice of MiCRM. By harnessing the synergistic capabilities of these technologies, stakeholders can provide novel prospects for innovation and ongoing enhancement of risk management procedures in the construction sector.
References
[1]. Darko, Amos, et al. (2020) “Building Information Modeling (BIM)-Based Modular Integrated Construction Risk Management-Critical Survey and Future Needs.” COMPUTERS IN INDUSTRY, vol. 123.
[2]. Goodier, C., Gibb, A. (2007). Future opportunities for offsite in the UK. Constr. Manag. Econ. 25 (6). pp. 585–595.
[3]. Baloi, D., Price, A.D. (2003). Modelling global risk factors affecting construction cost performance. Int. J. Proj. Manag. 21 (4), pp. 261–269.
[4]. Ameyaw, E. E., Hu, Y., Shan, M., Chan, A., & Le, Y. (2016). Application of Delphi method in construction engineering and management research: A Quantitative perspective. Journal of Civil Engineering and Management, 22. pp. 991–1000
[5]. Drawbotics. (2020). The BIM Revolution in Building Management (Apr. 4, 2020) https://blog.drawbotics.com/2018/11/07/the-bim-revolution-in-buildingmanagement/.
[6]. Qihua Tong. (2021). Application of BIM technology in metro construction progress risk management. Modern Transportation Technology Research, Volume 3, Issue 3.
[7]. Zou, Y., Kiviniemi, A., & Jones, S. (2015). BIM-based Risk Management: Challenges and Opportunities. Engineering.
[8]. Zhang, L., Wu, X., Skibniewski, M. J., Zhong, J. & Lu, Y. (2014). Bayesian-network-based safety risk analysis in construction projects. Reliability Engineering & System Safety. 131. pp. 29-39.
[9]. Kazi, A. S. (2005). Knowledge management in the construction industry: A socio-technical perspective, IGI Global. Khoshgoftaar, T. M. & Lanning, D. L. (1995). A neural network approach for early detection of program modules having high risk in the maintenance phase. Journal of Systems and Software. 29. pp. 85-91.
Cite this article
Cui,B. (2024). BIM - based modular integrated construction risk management. Applied and Computational Engineering,70,8-13.
Data availability
The datasets used and/or analyzed during the current study will be available from the authors upon reasonable request.
Disclaimer/Publisher's Note
The statements, opinions and data contained in all publications are solely those of the individual author(s) and contributor(s) and not of EWA Publishing and/or the editor(s). EWA Publishing and/or the editor(s) disclaim responsibility for any injury to people or property resulting from any ideas, methods, instructions or products referred to in the content.
About volume
Volume title: Proceedings of the 2nd International Conference on Functional Materials and Civil Engineering
© 2024 by the author(s). Licensee EWA Publishing, Oxford, UK. This article is an open access article distributed under the terms and
conditions of the Creative Commons Attribution (CC BY) license. Authors who
publish this series agree to the following terms:
1. Authors retain copyright and grant the series right of first publication with the work simultaneously licensed under a Creative Commons
Attribution License that allows others to share the work with an acknowledgment of the work's authorship and initial publication in this
series.
2. Authors are able to enter into separate, additional contractual arrangements for the non-exclusive distribution of the series's published
version of the work (e.g., post it to an institutional repository or publish it in a book), with an acknowledgment of its initial
publication in this series.
3. Authors are permitted and encouraged to post their work online (e.g., in institutional repositories or on their website) prior to and
during the submission process, as it can lead to productive exchanges, as well as earlier and greater citation of published work (See
Open access policy for details).
References
[1]. Darko, Amos, et al. (2020) “Building Information Modeling (BIM)-Based Modular Integrated Construction Risk Management-Critical Survey and Future Needs.” COMPUTERS IN INDUSTRY, vol. 123.
[2]. Goodier, C., Gibb, A. (2007). Future opportunities for offsite in the UK. Constr. Manag. Econ. 25 (6). pp. 585–595.
[3]. Baloi, D., Price, A.D. (2003). Modelling global risk factors affecting construction cost performance. Int. J. Proj. Manag. 21 (4), pp. 261–269.
[4]. Ameyaw, E. E., Hu, Y., Shan, M., Chan, A., & Le, Y. (2016). Application of Delphi method in construction engineering and management research: A Quantitative perspective. Journal of Civil Engineering and Management, 22. pp. 991–1000
[5]. Drawbotics. (2020). The BIM Revolution in Building Management (Apr. 4, 2020) https://blog.drawbotics.com/2018/11/07/the-bim-revolution-in-buildingmanagement/.
[6]. Qihua Tong. (2021). Application of BIM technology in metro construction progress risk management. Modern Transportation Technology Research, Volume 3, Issue 3.
[7]. Zou, Y., Kiviniemi, A., & Jones, S. (2015). BIM-based Risk Management: Challenges and Opportunities. Engineering.
[8]. Zhang, L., Wu, X., Skibniewski, M. J., Zhong, J. & Lu, Y. (2014). Bayesian-network-based safety risk analysis in construction projects. Reliability Engineering & System Safety. 131. pp. 29-39.
[9]. Kazi, A. S. (2005). Knowledge management in the construction industry: A socio-technical perspective, IGI Global. Khoshgoftaar, T. M. & Lanning, D. L. (1995). A neural network approach for early detection of program modules having high risk in the maintenance phase. Journal of Systems and Software. 29. pp. 85-91.