1. Introduction
The energy crisis and environmental pollution are two major challenges faced by countries around the world today. Pure electric vehicles (PEVs), with their energy-saving and environmentally friendly features, have become an inevitable trend in the future development of the automotive industry[1]. The batteries of electric vehicles are not only central to the development of PEVs but also represent a key integration point between the power industry and the automotive sector[2]. The Battery Management System (BMS) is an essential component within electric vehicles, responsible for monitoring, controlling, and protecting the charging and discharging processes of the batteries. Failures in the BMS can pose a threat to vehicle performance and driving safety. Therefore, developing a fault analysis and diagnostic system for electric vehicle BMS has significant practical importance. Such a system can collect real-time battery performance data and utilize advanced data analysis and artificial intelligence technologies to quickly and accurately pinpoint faults in the battery system, providing robust support for subsequent maintenance. This contributes positively to enhancing the reliability, safety, and economy of electric vehicles.
1.1. Domestic Development Status
Although China's BMS industry started relatively late, it has made certain progress in recent years, particularly in the reliability of data collection, the accuracy of State of Charge (SOC) estimation, balancing technology, and safety management. Domestic companies such as BYD and CATL have been continuously increasing their market share, demonstrating a latecomer advantage. The domestic BMS industry chain is gradually maturing, from materials, integrated circuits, printed circuit boards, to BMS production, and downstream applications, all of which have been involved and planned. This is due to the promotion of national policies, and the new energy automotive industry has ushered in rapid development. As one of the core components, BMS has also received corresponding attention and investment. It is worth noting that the trend of cooperation between domestic universities and enterprises in the development of BMS is evident, such as the cooperation between Beijing Jiaotong University and Huizhou Yieneng Electronics, and the cooperation between Harbin Guantao and Harbin Institute of Technology and Beijing Institute of Technology, etc[3]. These cooperations have promoted the innovation and application of BMS technology.
1.2. International Development Status
Overseas markets, especially the United States, Japan, South Korea, and Germany, have mature technology and products in the BMS field[4,5]. Companies such as SK, DENSO, Preh, LG Chem, Toyota, Bosch, and Tesla hold a dominant position in the global market. Their BMS technology continues to innovate in fault diagnosis, predictive maintenance, and wireless communication, striving to improve the system's intelligence and self-learning capabilities. Moreover, they are moving towards integrated and modular design directions, integrating more advanced sensors, such as monitoring technology based on Electrochemical Impedance Spectroscopy (EIS), to provide more comprehensive information on the health status of the battery. In addition, they are more active in the standardization and international cooperation of BMS, committed to promoting the unification of technical standards and safety specifications worldwide.
2. Introduction to the BMS System
2.1. Components
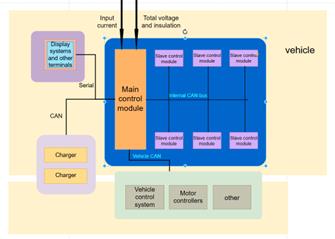
Figure 1. BMS system composition diagram
The Battery Management System (BMS) is designed for the safe monitoring and effective management of battery packs, aiming to enhance the efficiency of battery use, thereby increasing the driving range, extending the service life, and reducing operational costs. It further improves the reliability of the battery pack and has become an indispensable core component of electric vehicles. The BMS primarily consists of the power battery casing, battery pack, main control module, slave control modules, high-voltage monitoring module, low-voltage battery management system, current sensors, temperature sensors, internal CAN bus of the battery, and the main relay, among other components.
2.2. Basic Working Principle
The core working principle of the BMS can be summarized in the following continuous steps: Initially, the data acquisition circuitry is responsible for collecting information related to the state of the battery, including but not limited to key parameters such as voltage, current, and temperature. Subsequently, this data is transmitted to the Electronic Control Unit (ECU), where it undergoes thorough data processing and analysis. Based on the results of the analysis, the ECU formulates and issues precise control commands to the relevant functional modules within the system. These functional modules then respond accordingly, performing required operations such as adjusting charging and discharging strategies, activating thermal management mechanisms, or executing battery balancing. Additionally, the BMS is responsible for effectively conveying the state of the battery and system events to the vehicle's external management system for real-time monitoring and historical recording.
2.3. Main Functions of BMS
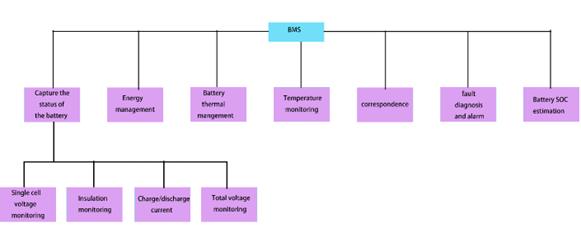
Figure 2. Main Functions of BMS
3. Introduction to BMS Faults and Common Fault Analysis
3.1. Classification of BMS Faults
3.1.1. Hardware Faults
Hardware faults account for a significant proportion of BMS issues, and their identification and repair are crucial for system stability[2]. For instance, sensor malfunctions can lead to inaccurate monitoring of battery status, thereby affecting charging strategies and battery life. Circuit faults, such as short circuits or open circuits, may directly threaten battery safety[3]. Failures in power devices, such as the damage to MOSFETs, can prevent normal charging and discharging of the battery, impacting the normal operation of electric vehicles.
3.1.2. Software Faults
Software faults in BMS can stem from logical errors or inaccurate data processing. These errors may lead to improper responses like overcharging or over-discharging, which can reduce battery lifespan and trigger safety issues. Incorrect SOC or SOH estimations can misguide BMS decision-making, resulting in inappropriate battery usage and maintenance. Addressing these faults is essential for maintaining battery health and safety.
3.1.3. Communication Faults
Communication faults can impede the exchange of information between the BMS and other vehicle systems, affecting overall vehicle performance. Interface faults may cause data transmission interruptions, while protocol errors can lead to data parsing failures. Additionally, electromagnetic interference issues can destabilize communication signals, affecting the BMS's real-time monitoring capabilities.
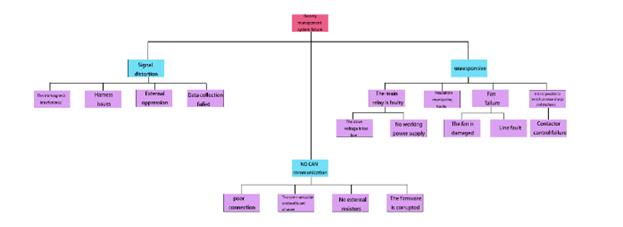
Figure 3. Fault Summary Diagram
3.2. Determination of Fault Priority
Currently, BMS faults are categorized into three levels: Level 1 faults are severe and can cause issues such as fires, explosions, and electric shocks, leading to significant damage to the power battery and even total vehicle loss; Level 2 faults are generally hardware-related, including issues like the cessation of regenerative braking, charging stoppage, and the power battery not functioning properly[6]. Upon detection, these issues require system inspection and troubleshooting, and hardware replacement may be necessary in severe cases; Level 3 faults are minor and generally do not pose a serious threat, but they may restrict certain functions, such as power and acceleration. These are often influenced by environmental temperature changes that can affect the power battery and cause it to degrade.
Table 1. Fault Severity Grading
The severity of the failure in this document |
|
effect |
|
suggestion |
|
3 (Warning) |
|
Minor |
|
This level of fault is minor and may go unnoticed by the driver. The vehicle is allowed to continue operation, but the driver should be alerted. |
|
2 (Alert) |
|
Moderate |
|
This level of fault is more serious and can affect vehicle performance or battery health, leading to noticeable degradation of some vehicle functions. |
|
1(Emergency Power-off) |
|
Severe |
|
This is a very high level of fault involving safety issues. The BMS must cut off the contactor in any mode. |
|
3.3. Fault Instance Analysis and Handling
3.3.1. CAN Communication Fault
The BMS communicates battery data to the VCU via the CAN bus. CAN bus issues can reduce vehicle performance and safety. Troubleshooting begins with inspecting signal lines and connections. If these are intact, use a DC multimeter to check the CANH and CANL voltages for a normal 1.5V reading. Abnormal voltages suggest a BMS hardware problem that might require repair or replacement.
3.3.2. Cooling Fan Malfunction
The cooling fan in the BMS is responsible for effectively dissipating the heat generated by the battery to maintain it within a safe temperature range. A malfunctioning fan can lead to abnormal increases in battery temperature, increasing the risk of thermal runaway and affecting battery performance and life. Causes of fan failure may include electronic control unit (ECU) malfunction, motor damage, power supply issues, thermal protection activation, or control signal interruption. To ensure effective cooling of the BMS, real-time monitoring of the fan's operating status is essential. Fault detection can be achieved through current monitoring, speed detection, or detection of abnormal temperature rises. Once a fan fault is detected, the fault diagnosis procedure should be immediately initiated to determine the cause and take appropriate measures. Possible strategies include fault indication, system reconfiguration, activation of backup cooling mechanisms, or emergency shutdown to prevent battery overheating.
3.3.3. Main Relay Failure
The main relay in a BMS is crucial for the operational safety of electric vehicles. Failures can cause severe issues like over-discharge, continuous current, and charging failure, disrupting vehicle function. Common failure modes include contactor sticking, wear, coil failure, mechanical issues, and ECU malfunction. Diagnosis involves resistance testing, current monitoring, sound analysis, temperature checks, and fault code analysis. Upon detecting a fault, immediate actions like isolation, system reconfiguration, fault indication, data logging, and repair or replacement are critical to maintain system safety and stability.
4. Fault Analysis of BMS
4.1. Qualitative Analysis Methods
Qualitative analysis plays a foundational role in the fault diagnosis of BMS, relying primarily on the accumulation of professional knowledge and experience[7]. Through Fault Mode Recognition (FMR), potential fault types such as overcharging, over-discharging, or short circuits can be identified. Expert systems simulate the decision-making process of experts, using rules from a knowledge base to logically infer and categorize faults. Fault Tree Analysis (FTA) constructs logical models to systematically trace the causes of faults, revealing potential paths to their occurrence. Additionally, historical case analysis refines common characteristics of faults from past events, providing referential insights for the diagnosis of current faults.
4.2. Quantitative Analysis Methods
Quantitative analysis methods achieve a quantified assessment of the impact and probability of faults in BMS fault diagnosis through numerical data and statistical techniques[7]. Failure Modes, Effects, and Diagnostic Analysis (FMEDA) statistically evaluates the failure probability of BMS components by collecting and analyzing failure data. Real-time fault detection algorithms, such as the Kalman filter, extract fault characteristics from sensor data, enabling quantitative fault identification. Statistical Process Control (SPC) uses statistical tools like control charts to monitor the operation of the BMS, identifying and quantifying anomalies in the process. Electrochemical Impedance Spectroscopy (EIS) and synchronized voltage-current reading techniques provide data support for precise fault diagnosis by quantitatively analyzing the internal resistance and state of the battery.
The advantages and disadvantages of these two methods are not absolute but depend on the specific application scenario and available resources. When data is abundant and models are accurate, quantitative analysis methods are superior due to their precision and predictive capabilities. However, in situations where data is insufficient or rapid diagnosis is required, qualitative analysis methods are more suitable due to their flexibility and reliance on expert experience[8]. In practical applications, both methods are often used in combination to leverage their respective strengths. For example, qualitative analysis can be used to quickly identify potential fault patterns, followed by quantitative analysis to further verify and quantify the impact of the faults.
4.3. Fault Diagnosis Techniques of BMS
The most widely applied fault diagnosis techniques are primarily model-based fault diagnosis and data-driven fault diagnosis. However, data-driven fault diagnosis requires a large amount of historical data for training samples, and its computational load is significant. Model-based fault diagnosis methods, on the other hand, can monitor transient processes and detect early minor abrupt and gradual faults, which have garnered widespread attention in the international academic and industrial communities in recent years. Therefore, model-based fault diagnosis will become increasingly important.
4.4. Model-Based Fault Diagnosis
The application of model-based fault diagnosis methods in the Battery Management System (BMS) is a technique that identifies, locates, and predicts potential faults in batteries and management systems by constructing and analyzing mathematical models[9]. In the model establishment phase, developing a mathematical model that describes the dynamic behavior and characteristics of the battery is crucial. The parameter identification process ensures that the model parameters match the actual system behavior, and residual generation reveals potential inconsistencies by comparing system outputs with model predictions. Subsequently, fault detection and isolation use residual signal analysis to determine the existence and location of faults. Fault prediction relies on the model's predictive capabilities to monitor trends in system parameters and provide early warnings of future faults. Finally, model validation and updating are key steps to ensure that the fault diagnosis system adapts to battery aging and environmental changes.
5. Outlook
With the rapid development of cutting-edge technologies such as data collection, image processing, artificial intelligence, and big data analysis, the fault diagnosis technology for power battery systems is undergoing revolutionary progress. The introduction of new sensing technologies has greatly expanded the entry points for fault diagnosis, promoting the development of sensor technology towards precision and multidimensionality, thereby enhancing the ability to monitor and maintain battery systems from all aspects and angles[10]. Intelligent fault diagnosis technology, by integrating various diagnostic methods based on knowledge, models, and data-driven approaches, has improved the accuracy and efficiency of fault identification. Moreover, the application of end-to-cloud integrated technology, combining the edge computing capabilities of onboard terminals with the analytical capabilities of cloud-based big data platforms, provides dual-layer protection for the safe management of battery systems, achieving health monitoring and fault diagnosis throughout the entire lifecycle of power batteries[6]. Online early warning methods, based on massive amounts of real vehicle operation data, have effectively prevented the occurrence of thermal runaway accidents through the establishment of thermal runaway prediction models, marking a leap in fault diagnosis technology from mere alarms to early warning and proactive control.
6. Summary
This paper first introduces the basic concepts of the Battery Management System (BMS), including its composition, working principles, and main functions. Subsequently, the article defines the relevant concepts of BMS faults and constructs a fault classification framework, categorizing faults into different levels. It further analyzes the characteristics and handling measures of common faults[1]. In the comparative analysis section, the paper discusses the features of qualitative and quantitative analysis methods and analyzes model-based and data-driven diagnostic technologies tailored to the characteristics of power battery systems. The paper focuses on a detailed discussion of model-based diagnostic technology and evaluates the advantages and applicability of current fault diagnosis methods. Finally, the article summarizes the development trends of fault diagnosis technology, pointing out that model-based diagnostic technology will become increasingly important in the future due to its accuracy and depth. With the development of artificial intelligence and big data technologies, fault diagnosis will evolve from passive alarms to proactive early warning and forward-looking control.
References
[1]. Lu, D. (2024). Analysis of common faults in power battery management system of new energy vehicles.Automobile Maintenance and Repair, 2: 70-72.
[2]. Bian, L., & Zu, Q. (2018). Fault analysis of power battery management system for pure electric vehicles. Automobile and Driving Maintenance (Maintenance Edition), 12: 90-91.
[3]. Liu, C., Lin, L., & Xu, H. (2018). Research on fault analysis and self-protection technology of battery system. Agricultural Equipment & Vehicle Engineering, 56(8): 9-12.
[4]. Zhang, Y. (2019). Analysis of BAIC power battery system and fault cases. China New Technology and Products, 12: 19-20.
[5]. Wang, H. (2023). Fault diagnosis analysis of power battery management system. Automobile and New Power, 3: 79-82.
[6]. Zhao, H., & Han, Y. (2016). Fault analysis of battery management system for pure electric vehicles. Shandong Industrial Technology, 7: 61.
[7]. Wang, L. (2018). Analysis of fault diagnosis methods for electric vehicle lithium battery management system. Practical Automobile Technology, 15: 18-19.
[8]. Tan, F. (2015). Research and implementation on fault diagnosis of vehicle power lithium-ion battery system. Thesis of Beijing Institute of Technology.
[9]. Xiao, Y. (2018). Design of fault analysis and processing system for power battery pack. Thesis of University of Electronic Science and Technology of China.
[10]. Yang, Q., Kang, X., Gao, M., et al. (2024). Design and implementation of fault analysis and diagnostic system for electric vehicle battery management system. China Equipment Engineering, 6: 188-190.
Cite this article
Su,R.;Lin,Z. (2024). A comprehensive review of BMS fault analysis in pure electric vehicles. Applied and Computational Engineering,89,94-100.
Data availability
The datasets used and/or analyzed during the current study will be available from the authors upon reasonable request.
Disclaimer/Publisher's Note
The statements, opinions and data contained in all publications are solely those of the individual author(s) and contributor(s) and not of EWA Publishing and/or the editor(s). EWA Publishing and/or the editor(s) disclaim responsibility for any injury to people or property resulting from any ideas, methods, instructions or products referred to in the content.
About volume
Volume title: Proceedings of the 2nd International Conference on Functional Materials and Civil Engineering
© 2024 by the author(s). Licensee EWA Publishing, Oxford, UK. This article is an open access article distributed under the terms and
conditions of the Creative Commons Attribution (CC BY) license. Authors who
publish this series agree to the following terms:
1. Authors retain copyright and grant the series right of first publication with the work simultaneously licensed under a Creative Commons
Attribution License that allows others to share the work with an acknowledgment of the work's authorship and initial publication in this
series.
2. Authors are able to enter into separate, additional contractual arrangements for the non-exclusive distribution of the series's published
version of the work (e.g., post it to an institutional repository or publish it in a book), with an acknowledgment of its initial
publication in this series.
3. Authors are permitted and encouraged to post their work online (e.g., in institutional repositories or on their website) prior to and
during the submission process, as it can lead to productive exchanges, as well as earlier and greater citation of published work (See
Open access policy for details).
References
[1]. Lu, D. (2024). Analysis of common faults in power battery management system of new energy vehicles.Automobile Maintenance and Repair, 2: 70-72.
[2]. Bian, L., & Zu, Q. (2018). Fault analysis of power battery management system for pure electric vehicles. Automobile and Driving Maintenance (Maintenance Edition), 12: 90-91.
[3]. Liu, C., Lin, L., & Xu, H. (2018). Research on fault analysis and self-protection technology of battery system. Agricultural Equipment & Vehicle Engineering, 56(8): 9-12.
[4]. Zhang, Y. (2019). Analysis of BAIC power battery system and fault cases. China New Technology and Products, 12: 19-20.
[5]. Wang, H. (2023). Fault diagnosis analysis of power battery management system. Automobile and New Power, 3: 79-82.
[6]. Zhao, H., & Han, Y. (2016). Fault analysis of battery management system for pure electric vehicles. Shandong Industrial Technology, 7: 61.
[7]. Wang, L. (2018). Analysis of fault diagnosis methods for electric vehicle lithium battery management system. Practical Automobile Technology, 15: 18-19.
[8]. Tan, F. (2015). Research and implementation on fault diagnosis of vehicle power lithium-ion battery system. Thesis of Beijing Institute of Technology.
[9]. Xiao, Y. (2018). Design of fault analysis and processing system for power battery pack. Thesis of University of Electronic Science and Technology of China.
[10]. Yang, Q., Kang, X., Gao, M., et al. (2024). Design and implementation of fault analysis and diagnostic system for electric vehicle battery management system. China Equipment Engineering, 6: 188-190.