1. Introduction
In retrospect, the concepts of gas turbines are proposed in early 20th century. The development of gas turbines is closely related to the progress of the aviation industry [1]. Early gas turbines were mainly used for aircraft engines, but as technology advanced, they also found widespread applications in the power generation sector [2, 3]. In the past few decades, gas turbine technology has made significant progress. Improvements in thermal efficiency, reduction in emissions, and enhancements in reliability and durability have made gas turbines an attractive choice for power generation and propulsion applications [4].
In recent years, research on gas turbines has mainly focused on improving performance, reducing emissions, and expanding fuel flexibility. Advanced manufacturing technologies have been used to manufacture gas turbine components with complex geometries and improved cooling characteristics [5, 6]. The ongoing ceramic-based composite materials has enabled them to operate at higher temperatures, i.e., improving efficiency [7]. Considerable work has also been done in reducing emissions. Technologies such as pre-combustion carbon dioxide capture and post-combustion treatment are proposed in order to reduce CO2 emissions from gas turbines [8, 9]. Additionally, gas turbines have been modified to use alternative fuels such as hydrogen to further reduce emissions [10].
Despite significant advancements in gas turbine technology, challenges still exist in terms of efficiency, emissions, and fuel flexibility. This paper aims to comprehensively analyze the basic principles of gas turbines, introduce state-of-the-art gas turbine facilities, explore the latest applications, and discuss the limitations of current research and future prospects. The structure of this paper is as follows. Section 2 describes the basic definition, classification, and working principle of gas turbines. Section 3 details the fundamental principles of gas turbines. Section 4 introduces the most advanced gas turbine facilities. Section 5 explores the latest applications of gas turbines. Section 6 analyzes the limitations of current research and looks ahead to future research directions. Finally, Section 7 summarizes the main findings and contributions of the paper.
2. Engine description
The gas turbine is a rotary engine that generates power or thrust by combusting fuel and utilizing the gas flow produced by thermal energy to drive turbine blades. Gas turbines mainly consist compressor, combustion chamber, and turbine [11, 12]. The compressor is one of the key components, which is responsible for compressing the air entering it (seen from Fig. 1). In axial-flow compressors, air flows along the axis of the compressor rotor and is compressed through alternating rows of stationary and rotating blades. In centrifugal compressors, air flows from the center of the compressor towards the periphery, being accelerated and compressed simultaneously. The compression process increases the pressure and temperature. To reduce pollutant emissions, modern gas turbines typically use low-NOx combustion chambers, employing techniques such as staged combustion and premixing to suppress the formation of nitrogen oxides. Combustion releases a large amount of thermal energy, further increasing the air temperature while generating better quality gases. After entering the turbine, driving the turbine blades to rotate and converting the energy of the gases into mechanical power. The gases expand and do work between the turbine blades, decreasing in temperature and pressure. The turbine drives the coaxial compressor, maintaining the operation of the gas turbine, with the remaining power used for electricity generation or propulsion [13]. To improve performance and reduce emissions, modern gas turbines employ a series of advanced technologies such as high-pressure ratio compressors, low-NOx combustion chambers, advanced cooling techniques, and high-temperature materials. These enable them to operate efficiently and cleanly under harsh conditions, meeting increasingly stringent energy efficiency and environmental protection requirements.
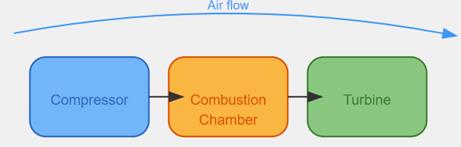
Figure 1. A sketch for the process of gas turbine (Photo/Picture credit: Original).
3. Gas turbine principles
The working principle of gas turbines is based on the Brayton cycle, which is an open thermodynamic cycle. Unlike ideal cycles such as the Carnot cycle, the Brayton cycle considers actual working fluid characteristics and engineering application limitations [14]. In an ideal Brayton cycle, air is first compressed isobarically (as depicted in Fig. 2). The compressed high-pressure air enters the combustion chamber, mixes with fuel, and completes combustion under isobaric conditions, further increasing in temperature. The high-temperature, high-pressure combustion gases then expand isentropically, doing work to drive the turbine rotation while decreasing in temperature and pressure. Finally, the gases release heat isobarically to the atmospheric environment, completing the cycle.
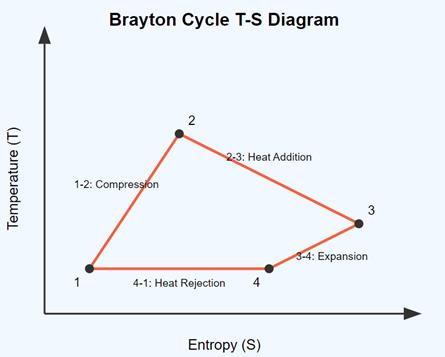
Figure 2. An illustration of the Brayton cycle (Photo/Picture credit: Original).
The compressor and turbine processes are not ideal isentropic processes and have irreversible losses, such as flow losses and blade boundary layer losses. Although the combustion process is close to isobaric, there is still some pressure loss. In addition, the actual cycle needs to consider the cooling requirements, e.g., turbine blade cooling. These factors cause the actual event with reducing the thermal efficiency [15]. To improve the efficiency of gas turbines, engineers have made various improvements and optimizations to the Brayton cycle. By adopting a regenerative cycle, which uses turbine exhaust to preheat the compressor outlet air, cycle efficiency can be significantly improved. Another improvement is intercooling, which introduces coolers between compressor stages to reduce the work consumption of the compression process. Additionally, advanced cycle modes such as combined cycle and humid cycle have been proposed, further tapping into the efficiency potential of gas turbines through more complex system arrangements and thermal management strategies [15].
Nevertheless, limited by material and process levels, the actual cycle efficiency of gas turbines is still significantly lower than that of the ideal Brayton cycle. To further improve gas turbine performance, researchers are exploring advanced materials, cooling technologies, and combustion strategies, striving to maximize the efficiency and power density of gas turbines while ensuring reliability and economic viability, and minimizing emissions and environmental impact [14, 15].
4. State-of-the-Art facilities
The most advanced gas turbine facilities employ multiple innovative technologies to enhance performance. Taking General Electric’s HA-class gas turbines as an example, they adopt advanced aerodynamic and thermodynamic designs and precise cooling technologies, significantly reducing cooling air consumption while increasing turbine inlet temperature. The HA-class gas turbines have a compressor pressure ratio of up to 23:1, with a single unit power output exceeding 500 megawatts, achieving over 63% power generation efficiency in combined cycle operation [16].
To achieve higher combustion temperatures and lower cooling losses, HA-class gas turbines extensively apply additive manufacturing (3D printing) technology. Combustion chamber nozzles and turbine blades are manufactured using 3D printing processes, integrating complex cooling channels internally. This not only improves cooling efficiency but also optimizes fuel atomization and mixing effects, reducing pollutant emissions [5]. Siemens’ SGT-8000H series gas turbines also represent the most advanced level. They use directionally solidified and single-crystal high-temperature alloy materials to manufacture turbine blades, providing excellent high-temperature strength and creep performance, enabling stable long-term operation at temperatures above 1500°C [17].
Fig. 3 illustrates the structural diagram of the Siemens SGT-8000H g. It adopts a compact arrangement of a 4-stage compressor, annular combustion chamber, and 4-stage turbine. By optimizing the airflow path and employing precise film cooling technology, it effectively enhances component efficiency and service life. To further increase combustion temperature and reduce nitrogen oxide emissions, Siemens has applied advanced dry low-NOx combustion technology in the SGT-8000H gas turbine. By precisely controlling the mixing ratio, stable combustion is achieved under relatively low equivalence ratio conditions, effectively reducing flame temperature and local hot spots, thereby significantly decreasing nitrogen oxide formation. The application of precise fuel staged injection and swirl combustion technology further optimizes the combustion process, achieving ultra-low emissions [11]. In addition to combustion and cooling technology innovations, advanced gas turbine facilities widely adopt modular design and digital control technologies. Standardized modular design significantly shortens manufacturing and installation cycles, reducing costs and maintenance workload. Advanced digital control systems can monitor the operating conditions of gas turbines in real-time, optimizing and adjusting combustion and cooling processes to ensure that gas turbines always operate efficiently in the best state [12].
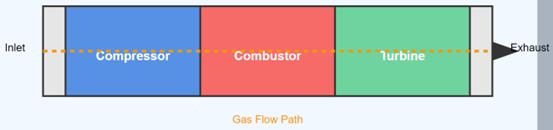
Figure 3. A sketch for Siemens SGT-8000H (Photo/Picture credit: Original).
5. Applications
Gas turbines, with their high efficiency, clean operation, and flexibility, have found widespread applications in power production and transportation sectors. They are often combined with steam turbines, which can fully utilize the waste heat, improving overall power generation efficiency. Taking the Kobe Rokko Island Power Plant in Japan as an example, this plant employs multiple GE 7HA-class gas turbines equipped with advanced gas-steam combined cycle systems, achieving a power generation efficiency exceeding 63%, ranking among the world’s top plants of its kind [18]. Apart from large-scale power plants, they are also implemented in distributed energy systems and combined heat and power projects. These systems are smaller in scale, closer to users, and can flexibly adjust according to electricity and heat demand, improving energy utilization efficiency. Gas turbines can burn clean fuels such as natural gas, offering significant environmental benefits compared to traditional coal-fired boilers.
In the transportation sector, gas turbines are core components of aircraft engines. Modern civil aviation engines generally adopt turbofan engines, where gas turbines are responsible for driving fans and compressors, providing thrust. With the rapid development of the aviation industry, higher requirements have been placed on the thrust-to-weight ratio, fuel efficiency, and emission performance of gas turbines. CFM International’s LEAP engine is a representative new-generation aviation gas turbine, employing 3D printed nozzles, ceramic matrix composites, and improved aerodynamic design, achieving ultra-low emissions while improving fuel efficiency [19].
Gas turbines are also widely applied in ship power systems, especially in scenarios such as warships and high-speed passenger ships that require high power density and speed performance. Compared to diesel engines, gas turbines start quickly and have high power density, enabling rapid deployment and maneuverability. The U.S. Navy’s Zumwalt-class destroyers adopt advanced gas turbine power systems, with two MT30 gas turbines providing main power, achieving a maximum speed exceeding 30 knots.
Fig. 4 shows the proportion of gas turbines in different application fields. The power generation sector accounts for the largest share at 65%, reflecting the important position of gas turbines as efficient and clean power generation equipment. The aviation sector accounts for 25%, representing another key application direction for gas turbines. The marine power sector has a relatively smaller share at 10%, but still possesses unique advantages and broad prospects in specific scenarios. With global energy transition and low-carbon economic development, gas turbines are expected to play a greater role in areas such as renewable energy grid integration, energy storage peak shaving, and fuel diversification. The application of new fuels such as hydrogen and synthetic gas in gas turbines will also be an important development direction in the future, helping to further reduce carbon emissions and maximize comprehensive benefits.
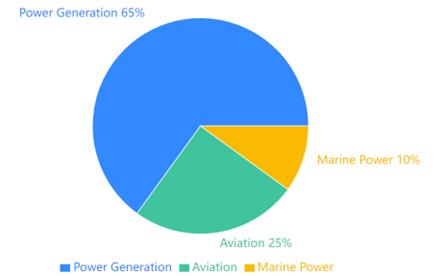
Figure 4. The proportion of gas turbines in different application fields (Photo/Picture credit: Original).
6. Limitations and prospects
Although gas turbine technology has made great strides in the past few decades, some limitations still exist. Currently, even the most advanced gas turbines have actual efficiencies significantly lower than theoretical limits, constrained by factors such as combustion temperature and cooling technology. While gas turbines are cleaner compared to traditional coal-fired boilers, they remain a significant source of greenhouse gases and pollutants. Moreover, traditional gas turbines have high fuel quality requirements, and their fuel adaptability needs improvement. Despite these limitations, the development prospects of gas turbine technology remain broad. In the future, high-temperature new materials, advanced cooling technologies, low-emission combustion, and new cycle modes will be research priorities, potentially driving breakthroughs in gas turbine efficiency, emissions, and fuel flexibility. The coupling of gas turbines with energy storage and carbon capture technologies will also become a hot topic, enhancing system flexibility and environmental performance. With technological advancements, gas turbines are expected to achieve comprehensive performance improvements in the future, becoming important power generation and propulsion devices that balance environmental protection, efficiency, and flexibility. In the context of energy transition and low-carbon development, gas turbines will play an increasingly important role, contributing to global sustainable development.
7. Conclusion
To sum up, this study comprehensively analyzes the principles and current applications of gas turbines. Through a systematic introduction of gas turbine working principles, thermodynamic cycle characteristics, and key components, it discusses the main technical approaches to improve their performance. The article focuses on analyzing the application of gas turbines in fields such as power generation, aviation, and marine, demonstrating their advantages of high efficiency, cleanliness, and flexibility. The study points out that although gas turbine technology has made significant progress, it still faces challenges in efficiency improvement, emission control, and fuel adaptability. In the future, breakthroughs in key technologies such as high-temperature materials, advanced cooling, and low-emission combustion will drive gas turbines to achieve higher performance. This research deepens the understanding of gas turbine technology and provides an important reference for engineering practice and innovative research.
References
[1]. Koff B L 2004 Gas turbine engines: from aviation propulsion to power generation and propulsion Aerospace Science and Technology vol 407 pp 658-664
[2]. Langston L S 2014 Gas turbines for electric power generation Technology Review Massachusetts Institute of Technology vol 814 pp 54-55
[3]. Nada T 2017 Performance characterization of different working fluids for an aviation turbine application Aviation p 18
[4]. Brooks F J 2000 GE gas turbine performance characteristics and development trends Engines vol 19 p 111
[5]. Navrotsky V, Graichen A and Brodin H 2015 Industrialization of 3D printing additive manufacturing for gas turbine components repair and manufacturing VGB PowerTech vol 12 pp 48-52
[6]. Sinha A, Swain B, Behera A, et al 2022 A review on the processing of aero-turbine blade using 3D print techniques Journal of Manufacturing and Materials Processing vol 6(1) p 16.
[7]. Perepezko J H 2009 The hotter the engine the better Science vol 3265956 pp 1068-1069
[8]. Li H, Ditaranto M and Berstad D 2011 Technologies for increasing CO2 concentration in exhaust gas from natural gas-fired power production with post-combustion amine-based CO2 capture Energy vol 362 pp 1124-1133
[9]. Giampaolo T 2019 Gas turbine handbook: principles and practices 5th ed Springer
[10]. Chiesa P, Lozza G and Mazzocchi L 2005 Using hydrogen as gas turbine fuel Journal of engineering for gas turbines and power vol 1271 pp 73-80
[11]. Noor M M, Tuan H A and Mishra P C 2022 Advances in Mechanical and Industrial Engineering: Proceedings of the International Conference on Advances in Mechanical and Industrial Engineering (ICAMIE 2020) p 15
[12]. Boyce M P 2011 Gas turbine engineering handbook Elsevier
[13]. Saravanamuttoo H I H, Rogers G F C and Cohen H 2001 Gas turbine theory Pearson education
[14]. Moran M J Shapiro H N Boettner D D and Bailey M B 2010 Fundamentals of engineering thermodynamics John Wiley & Sons
[15]. Horlock J H 2013 Advanced gas turbine cycles: a brief review of power generation thermodynamics Google Publications
[16]. Hood R L 2022 Embodied Energy Geographies: An Exploration of Fracked Landscapes in the Ohio River Valley West Virginia University
[17]. Susta M R 2004 Siemens SGT-8000H: efficient and environmentally friendly Modern Power Systems vol 2411 pp 25-28
[18]. Kanoh T, Takehara T and Yoshida K 2018 High efficiency gas turbine combined cycle system of Rokko Island power station Mitsubishi Heavy Industries Technical Review vol 551 pp 1-5
[19]. Jagtap S S 2019 Systems evaluation of subsonic hybrid-electric propulsion concepts for NASA N+ 3 goals and conceptual aircraft sizing International Journal of Automotive and Mechanical Engineering vol 164 pp 7259-7286
Cite this article
Zhou,S. (2024). Analysis of the Principle of Gas Turbine and State-of-art Applications. Applied and Computational Engineering,98,35-40.
Data availability
The datasets used and/or analyzed during the current study will be available from the authors upon reasonable request.
Disclaimer/Publisher's Note
The statements, opinions and data contained in all publications are solely those of the individual author(s) and contributor(s) and not of EWA Publishing and/or the editor(s). EWA Publishing and/or the editor(s) disclaim responsibility for any injury to people or property resulting from any ideas, methods, instructions or products referred to in the content.
About volume
Volume title: Proceedings of the 2nd International Conference on Functional Materials and Civil Engineering
© 2024 by the author(s). Licensee EWA Publishing, Oxford, UK. This article is an open access article distributed under the terms and
conditions of the Creative Commons Attribution (CC BY) license. Authors who
publish this series agree to the following terms:
1. Authors retain copyright and grant the series right of first publication with the work simultaneously licensed under a Creative Commons
Attribution License that allows others to share the work with an acknowledgment of the work's authorship and initial publication in this
series.
2. Authors are able to enter into separate, additional contractual arrangements for the non-exclusive distribution of the series's published
version of the work (e.g., post it to an institutional repository or publish it in a book), with an acknowledgment of its initial
publication in this series.
3. Authors are permitted and encouraged to post their work online (e.g., in institutional repositories or on their website) prior to and
during the submission process, as it can lead to productive exchanges, as well as earlier and greater citation of published work (See
Open access policy for details).
References
[1]. Koff B L 2004 Gas turbine engines: from aviation propulsion to power generation and propulsion Aerospace Science and Technology vol 407 pp 658-664
[2]. Langston L S 2014 Gas turbines for electric power generation Technology Review Massachusetts Institute of Technology vol 814 pp 54-55
[3]. Nada T 2017 Performance characterization of different working fluids for an aviation turbine application Aviation p 18
[4]. Brooks F J 2000 GE gas turbine performance characteristics and development trends Engines vol 19 p 111
[5]. Navrotsky V, Graichen A and Brodin H 2015 Industrialization of 3D printing additive manufacturing for gas turbine components repair and manufacturing VGB PowerTech vol 12 pp 48-52
[6]. Sinha A, Swain B, Behera A, et al 2022 A review on the processing of aero-turbine blade using 3D print techniques Journal of Manufacturing and Materials Processing vol 6(1) p 16.
[7]. Perepezko J H 2009 The hotter the engine the better Science vol 3265956 pp 1068-1069
[8]. Li H, Ditaranto M and Berstad D 2011 Technologies for increasing CO2 concentration in exhaust gas from natural gas-fired power production with post-combustion amine-based CO2 capture Energy vol 362 pp 1124-1133
[9]. Giampaolo T 2019 Gas turbine handbook: principles and practices 5th ed Springer
[10]. Chiesa P, Lozza G and Mazzocchi L 2005 Using hydrogen as gas turbine fuel Journal of engineering for gas turbines and power vol 1271 pp 73-80
[11]. Noor M M, Tuan H A and Mishra P C 2022 Advances in Mechanical and Industrial Engineering: Proceedings of the International Conference on Advances in Mechanical and Industrial Engineering (ICAMIE 2020) p 15
[12]. Boyce M P 2011 Gas turbine engineering handbook Elsevier
[13]. Saravanamuttoo H I H, Rogers G F C and Cohen H 2001 Gas turbine theory Pearson education
[14]. Moran M J Shapiro H N Boettner D D and Bailey M B 2010 Fundamentals of engineering thermodynamics John Wiley & Sons
[15]. Horlock J H 2013 Advanced gas turbine cycles: a brief review of power generation thermodynamics Google Publications
[16]. Hood R L 2022 Embodied Energy Geographies: An Exploration of Fracked Landscapes in the Ohio River Valley West Virginia University
[17]. Susta M R 2004 Siemens SGT-8000H: efficient and environmentally friendly Modern Power Systems vol 2411 pp 25-28
[18]. Kanoh T, Takehara T and Yoshida K 2018 High efficiency gas turbine combined cycle system of Rokko Island power station Mitsubishi Heavy Industries Technical Review vol 551 pp 1-5
[19]. Jagtap S S 2019 Systems evaluation of subsonic hybrid-electric propulsion concepts for NASA N+ 3 goals and conceptual aircraft sizing International Journal of Automotive and Mechanical Engineering vol 164 pp 7259-7286