1. Introduction
The invention of the Newcomen atmospheric steam engine (1712) in the 18th century, and the later promulgation of James Watt's patent on the separated condenser (1769) and the further improvement and transformation of the steam engine (1782), made Sade Cano demonstrate the concept of universal heat engine in 1824 on this basis [1]. Thanks to the rapid improvement of thermodynamics in the first half of the 19th century, the new concept of thermal energy was demonstrated, which combined the next 50 years of theoretical research with actual heat engine manufacturing, opening a period of glorious development in the field of heat engine [2].
When the basic operation process of the heat engine is determined, because the heat engine needs to be widely and safely arranged in large and small parts of the social production operation, all sectors of society begin to pay attention to the need to ensure the smoothness and stability of the operation of the heat engine. Coating coverage on the heat engine has become an excellent solution to meet the above needs. Law. Among many types of heat engines, such as gas turbines, need to be exposed to unsuitable environments for continuous work, which makes the development of applied coating materials crucial [3]. The manufacturing of modern heat engine is indispensable to apply the protective coating system to ensure that the heat engine can be used effectively for a long time. The coating development of the heat engine has gone through the following processes; the early hot engine coating is mostly metal-based coating, from the aluminum and galvanized layer at the beginning to the coating of alloys and metal compounds. With the development of simple ceramic base materials, ceramic coatings are also covered on the hot engine of the same period. Since then, the types of hot engine coatings have gradually increased. It aims to improve the high temperature tolerance, friction tolerance, thermal barrier, oxidation barrier and other properties of the heat engine coating. The composite thermal environment barrier coating composed of different types of coatings has become the guide for development. For example, advanced ceramic-based coatings are envisaged to be completed in the supersonic vehicle engine planned by NASA. The purpose of efficiency and reliability [4].
The purpose of the separate display of different bases of heat engine coatings is set to summaries their characteristics and the use of coatings that are originally limited in use can be identified and analyzed by people, so that people can cover different heat engines across types. For example, high-quality aviation turbine coatings are applied to the engines of household cars, aiming to Develop the popularization and benefit of special technologies. Next, the characteristics and envisaged applications of the metal-based coating, ceramic-based coating and polymerization-based coating of the heat engine will be shown separately, and then make a brief comparison to make a prospect of the future evolution potential of the heat-based coating.
2. Metal-based coating
The thermal machine coating of metal-based composite materials was tried to cover the thermal machine when the concept of coating was proposed. After the epidemic (COVID-19), the global steel consumption of steel has stimulated global steel production due to economic recovery, with a year-on-year increase of 3.7% in 2021. At the same time, with the updating of new cognition and technology in the steel smelting industry, the productivity of the modern thermal spray coating industry is gradually improved. Therefore, steel-based coatings have once again become the best choice for many basic coatings with their simple casting process and low casting costs [5]. Thermal machine metal-based coating technology can further benefit under this trend. However, the coarse steel-based coating of the foundation is still challenged by long-term continuous corrosion and high-temperature combustion of the thermal machine. As a part that only has a marginal impact on the performance of the thermal machine, the coating can only be deeply explored continuously, in order to make the thermal machine work effectively in harsher environments.
It is necessary to consider the use of steel coatings of different processes from the needs of thermal machines. In the previous introduction, the basic requirements of the thermal machine in terms of coating have been clarified. After further understanding the special requirements of the target coating, consider all aspects of casting. After iron ore mining, first consider the basic degree of grinding and fineness. Secondly, during the smelting process, consider the amount of carbon and oxygen injected to control the degree of softness and hardness, oxidation and the degree of toughness. At the same time, consider whether to add other metal elements and modify the surface or internal structure to delay the aging of the thermal machine and reduce the subsequent the purpose of this.
History has proved that thermal spraying technology has an excellent effect on the manufacture of steel and other alloys. Thermal spraying technology can also be applied in the surface transformation of hot machine hard parts. Generally speaking, the thermal spraying process is related to molten or semi-molten particles with deposition effect. Particles are sprayed and splashed in the thermal environment, forming specific forms of micro-conforments, which are intertwined into a locked and integrated network structure. Compared with other coating technologies of metals, even if thermal spraying technology will have a wider deposition phenomenon, it can quickly complete a large area of coating coverage. Thermal spraying technology is also divided into many types, including flame spraying, explosive spraying, linear arc spraying, plasma spraying and HVOF coating spraying [5, 6].
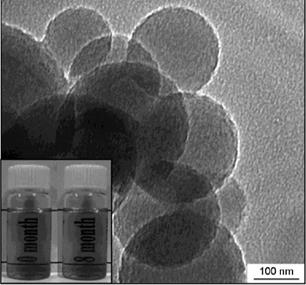
Figure 1. A typical TEM structure of PI coating [10].
3. Polymer-based coating
Polymer-based materials are outstanding in various environments for thermal machine requirements [7]. Polymers are widely used in pollution prevention in the commercial category, because they can be developed synthetically by chemical means, and the surface modification results are better than those of metal materials using rich functional groups. Polymer-based materials have a variety of spraying methods. In addition to simple physical adsorption technology, a series of chemical reactions can be carried out to meet special needs with the characteristics of organic matter. From the technical analogy on the anti-fouling coating, a comprehensive method of using cross-linking agents or gripping bonds can be used to produce qualified and suitable coatings [7]. In the hot machine Large-scale coverage on many parts.
PTFE is resistant to high temperatures in most cases and is increasingly valued in thermal engines in various industries. A basic manufacturing method involving the formation of a stable coating on polypropylene yarn. It is based on the ultra-thin and continuous uniform base coating on the surface of the yarn bundle. Then doped with sodium stearate to improve the stability of magnetite nanoparticles. The ultra-thin polytetrafluoroethylene coating has deeper potential. The ultra-film shows the results of AFM and the rich value of PTEF itself [8], which can be applied to engine parts, valves and seals that need anti-corrosion.
PI coating has the characteristics of composite materials of other textures and transmitting its own excellence. Steel, copper or aluminum and PI produce the behavior of mutual adhesion, and the mixed coating is affected by different degrees of PI [9]. Such an attempt is envisaged that the PI composite coating can be applied to the heating machine that requires the characteristics of metal-based materials and the characteristics of PI materials at the same time. PI is also resistant to high temperatures and has excellent electrical insulation performance, which meets the needs of aerospace thermal machines and new thermal machines for mixed electronic equipment. PI has a highly aromatic structure to support it as a high-quality material that enhances the high-temperature thermoplastic of carbon fiber. The preparation methods include primitive and direct high-temperature vapor deposition polymerization and PAA slurry for glorying and thermal curing (seen from Fig. 1) [10]. The coating composite of PI and carbon fiber is simple to make and suitable for large-scale production, which provides a promising solution for the design of high-strength carbon fiber used in the thermal machine.
4. Ceramic-based coating
For larger industrial operations such as power generation, ship gas turbines, mineral processing, etc., industrial heat engines need to withstand a high-temperature environment of at least more than 500°C in a series of industrial operations. The purpose of thermal barrier coating (TBC) is to effectively insulate heat and provide a stable thermal environment. In order to meet the effective operation of the thermal function in the harsh environment of industrial operation, the ceramic coating can achieve the excellent performance of TBC material: no melting phenomenon at high temperature, long-term heat resistance in cycle operation, and ensuring the integrity of the thermal machine in the corrosive environment and other major challenges [11]. The mechanical and corrosion stress effects of ceramic materials outside the work itself can still provide a good guarantee, which makes it a topic worth discussing in the field of thermal machine coating in the future.
Zirconium oxide has chemical properties and inactive properties. Its high melting point, high resistivity and low expansion coefficient are very representative in ceramic coatings. Its production method is the colloidal method to add Zr oxide to SiO2 solution, which is formed by spraying and drawing, and it is formed into fibers after drying. At the same time, there are also extrusion, impregnation and hydrolysis, etc. Zirconium oxide is used as TBC in gas turbines to reduce the substrate temperature.
The chrome-plated coating of appropriate thickness has a good protective effect. In the study of oxidative kinetics, it still has good oxidation resistance at high temperatures, which solves the problem of brittlement and oxidation caused by Zr alloy and liquid vapor at high temperatures [12]. These studies give a theoretical basis for the idea that composite ceramic coatings have further advantages in the application of thermal machines.
Plasma spraying is mentioned in the metal-based coating part. Similarly, this spraying method has the highest efficiency of plasma spraying technology on non-metallic ceramics (as given in Fig. 2) [13], and it can also effectively carry out surface strengthening and surface modification. This technology adopts DC-driven plasma arc as a heat source, and ceramic materials are sprayed at high speed at nanometer-level particles to the pretreated thermal machine components. High-precision particles enable it to effectively control scattering. At the same time, plasma spraying technology produces material nanoparticles with extraordinary performance in terms of thermal properties.
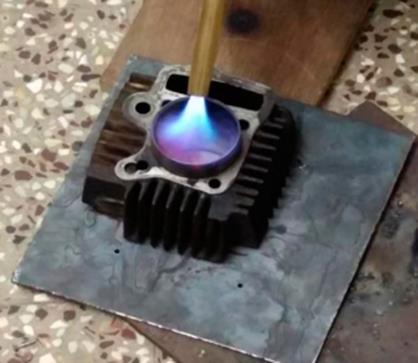
Figure 2. A sketch of Plasma spraying coating [13].
5. Conclusion
To sum up, the impact of coating on the thermal machine is specific. In point of views, the composite use of different types of coatings and different materials is the direction of future development. The specificity of various coating materials can be targeted under different working conditions, so that the new coating developed can effectively meet the needs of complex factors and multiple specificity mixing in the future, whether in industry, commercial or household.
References
[1]. Pacey A J 1974 Some early heat engine concepts and the conservation of heat The British Journal for the History of Science vol 7(2) pp 135-145.
[2]. Bryant L 1973 The role of thermodynamics in the evolution of heat engines Technology and culture vol14(2) pp152-165.
[3]. Hetmańczyk M, Swadźba L and Mendala B 2007 Advanced materials and protective coatings in aero-engines application Journal of achievements in Materials and manufacturing Engineering vol 24(1) pp 372-381.
[4]. Zhu D, Miller R and Fox D 2008 Thermal and environmental barrier coating development for advanced propulsion engine systems 48th AIAA/ASME/ASCE/AHS/ASC Structures, Structural Dynamics, and Materials Conference p 2130.
[5]. Singh S, Berndt C C, Raman R K S, Singh H and Ang A S M 2023 Applications and developments of thermal spray coatings for the iron and steel industry. Materials vol 16(2) p 516.
[6]. Sunitha K and Vasudev H. A short note on the various thermal spray coating processes and effect of post-treatment on Ni-based coatings. Materials Today: Proceedings vol 50 pp 1452-1457.
[7]. Maan A M C, Hofman A H, De Vos W and Kamperman M 2020 Recent Developments and Practical Feasibility of Polymer-Based Antifouling Coatings. Advanced Functional Materials vol 30(32) p 2000936.
[8]. Prorokova N and Vavilova S 2021 Properties of polypropylene yarns with a polytetrafluoroethylene coating containing stabilized magnetite particles. Coatings vol 11(7), p 830
[9]. Hicyilmaz A S and Bedeloglu A C 2021 Applications of polyimide coatings: A review. SN Applied Science vol 3(3) p 363.
[10]. Yuan H, Lu C, Zhang S and Wu G 2015 Preparation and characterization of a polyimide coating on the surface of carbon fibers New Carbon Materials vol 30(2) pp115-121.
[11]. Iqbal A and Moskal G 2023 Recent Development in Advance Ceramic Materials and Understanding the Mechanisms of Thermal Barrier Coatings Degradation Archives of Computational Methods in Engineering vol 30(8) pp 4855-4896.
[12]. Kashkarov E B, Sidelev D V, Syrtanov M S, Tang C and Steinbrück M 2020 Oxidation kinetics of Cr-coated zirconium alloy: Effect of coating thickness and microstructure Corrosion Science vol 175 p 108883.
[13]. Raja V K B, Ramasubramanian S, Sonawwanay P D, Palanikumar K, Reddy A S and Nemade A C 2022 Increasing heat transfer in 4-stroke SI engine fins by nanocoating International Journal of Ambient Energy vol 43(1) pp 6763-6771.
Cite this article
Deng,S. (2024). Application of Metal-based, Polymer-based and Ceramic-Based Composites in Thermal Engine. Applied and Computational Engineering,89,9-13.
Data availability
The datasets used and/or analyzed during the current study will be available from the authors upon reasonable request.
Disclaimer/Publisher's Note
The statements, opinions and data contained in all publications are solely those of the individual author(s) and contributor(s) and not of EWA Publishing and/or the editor(s). EWA Publishing and/or the editor(s) disclaim responsibility for any injury to people or property resulting from any ideas, methods, instructions or products referred to in the content.
About volume
Volume title: Proceedings of the 2nd International Conference on Functional Materials and Civil Engineering
© 2024 by the author(s). Licensee EWA Publishing, Oxford, UK. This article is an open access article distributed under the terms and
conditions of the Creative Commons Attribution (CC BY) license. Authors who
publish this series agree to the following terms:
1. Authors retain copyright and grant the series right of first publication with the work simultaneously licensed under a Creative Commons
Attribution License that allows others to share the work with an acknowledgment of the work's authorship and initial publication in this
series.
2. Authors are able to enter into separate, additional contractual arrangements for the non-exclusive distribution of the series's published
version of the work (e.g., post it to an institutional repository or publish it in a book), with an acknowledgment of its initial
publication in this series.
3. Authors are permitted and encouraged to post their work online (e.g., in institutional repositories or on their website) prior to and
during the submission process, as it can lead to productive exchanges, as well as earlier and greater citation of published work (See
Open access policy for details).
References
[1]. Pacey A J 1974 Some early heat engine concepts and the conservation of heat The British Journal for the History of Science vol 7(2) pp 135-145.
[2]. Bryant L 1973 The role of thermodynamics in the evolution of heat engines Technology and culture vol14(2) pp152-165.
[3]. Hetmańczyk M, Swadźba L and Mendala B 2007 Advanced materials and protective coatings in aero-engines application Journal of achievements in Materials and manufacturing Engineering vol 24(1) pp 372-381.
[4]. Zhu D, Miller R and Fox D 2008 Thermal and environmental barrier coating development for advanced propulsion engine systems 48th AIAA/ASME/ASCE/AHS/ASC Structures, Structural Dynamics, and Materials Conference p 2130.
[5]. Singh S, Berndt C C, Raman R K S, Singh H and Ang A S M 2023 Applications and developments of thermal spray coatings for the iron and steel industry. Materials vol 16(2) p 516.
[6]. Sunitha K and Vasudev H. A short note on the various thermal spray coating processes and effect of post-treatment on Ni-based coatings. Materials Today: Proceedings vol 50 pp 1452-1457.
[7]. Maan A M C, Hofman A H, De Vos W and Kamperman M 2020 Recent Developments and Practical Feasibility of Polymer-Based Antifouling Coatings. Advanced Functional Materials vol 30(32) p 2000936.
[8]. Prorokova N and Vavilova S 2021 Properties of polypropylene yarns with a polytetrafluoroethylene coating containing stabilized magnetite particles. Coatings vol 11(7), p 830
[9]. Hicyilmaz A S and Bedeloglu A C 2021 Applications of polyimide coatings: A review. SN Applied Science vol 3(3) p 363.
[10]. Yuan H, Lu C, Zhang S and Wu G 2015 Preparation and characterization of a polyimide coating on the surface of carbon fibers New Carbon Materials vol 30(2) pp115-121.
[11]. Iqbal A and Moskal G 2023 Recent Development in Advance Ceramic Materials and Understanding the Mechanisms of Thermal Barrier Coatings Degradation Archives of Computational Methods in Engineering vol 30(8) pp 4855-4896.
[12]. Kashkarov E B, Sidelev D V, Syrtanov M S, Tang C and Steinbrück M 2020 Oxidation kinetics of Cr-coated zirconium alloy: Effect of coating thickness and microstructure Corrosion Science vol 175 p 108883.
[13]. Raja V K B, Ramasubramanian S, Sonawwanay P D, Palanikumar K, Reddy A S and Nemade A C 2022 Increasing heat transfer in 4-stroke SI engine fins by nanocoating International Journal of Ambient Energy vol 43(1) pp 6763-6771.