1. Introduction
The skid-mounted system is defined as an integrated assembly system that is designed, manufactured, integrated, and tested using the skid-mounted method [1-3]. Compared with conventional systems, it exhibits unique manufacturing and integration approaches, as well as a distinct structural configuration. A detailed comparison between skid-mounted and conventional systems is presented in Table 1. Modern skid-mounted systems typically comprise one or multiple skids, each supported by an independent steel structural base. These skid units are capable of independently (or partially independently) performing specific functions within the system, thereby serving as the smallest independent modules of the skid system[4-7]. Skid-mounted systems are generally manufactured, integrated, and tested in a factory environment and subsequently transported to the site for installation either as a complete unit or as individual skid blocks[8,9].
System |
Design |
Manufacture |
Integration |
On-site installation |
Construction |
Assembly quality |
Maintenance |
Scalability |
conventional system |
Isolated design |
Isolated manufacturing, procurement |
On-site integration, commissioning |
Installation of each part on site |
Complex site construction and large. workload |
Poor construction quality |
Convenientmaintenance.,Large footprint area |
cannot be extended |
skid-mounted system |
Integration of manufacturing and design |
Manufacturing and procurement in parallel |
In-plant integration and commissioning |
On-site modular installation |
Simple on-site construction |
On-site assembly installation, good construction quality |
Convenientmaintenance, Integrated layout, compact structure |
Reservable interface, replaceable extension |
The skid-mounted system originated in industries with harsh working conditions, such as oil mining, in the early to mid-twentieth century. To minimize on-site operations, equipment required for operations was often mounted on a steel base and shipped directly to the site[10-12]. Since the 1970s, the application of skid-mounted systems has expanded significantly, finding widespread use in fields such as nuclear power plant exhaust gas treatment, petrochemicals, and natural gas development and so on[13-15].The development of skid-mounted systems in China started relatively late, with initial reliance on imports. In the early 1990s, domestically developed skid-mounted systems were successfully applied and commissioned in the petrochemical industry. With the advancement and application of new technologies, skid-mounted systems have gradually penetrated into process industries such as natural gas, water treatment, and pharmaceuticals. These systems have also evolved into large-scale, complex industrial systems that integrate equipment, piping systems, electrical systems, control systems, installation foundations, and other auxiliary systems.
2. Design and principles of skid-mounted system
Currently, there are no uniform design principles and requirements for skid-mounted systems, and the design methodology varies depending on the person in charge. Drawing on years of engineering experience, the author has summarized the common steps and key points in the design process of skid-mounted systems.
The design of conventional systems typically focuses solely on the process flow and system functionality, with limited consideration for manufacturing, transportation, installation, inspection, and maintenance. Moreover, collaboration among different disciplines is often restricted to pipeline layout and collision detection. In contrast, the skid-mounted approach is a multi-disciplinary, collaborative design method. Its design goals extend beyond merely ensuring the functionality of the process flow to encompass the entire life cycle, including manufacturing, procurement, transportation, integration, inspection, maintenance, and utilization.
The design process can be summarized into several key aspects, each requiring a multi-disciplinary approach and iterative feedback:1. function modularization and skid block division;2. Structural module design;3. Optimization of skid layout;4. Interface design;5. Skid-mounted transformation of the electrical and control systems. These components collectively ensure a comprehensive and integrated design strategy. For further details, refer to Figure 1.
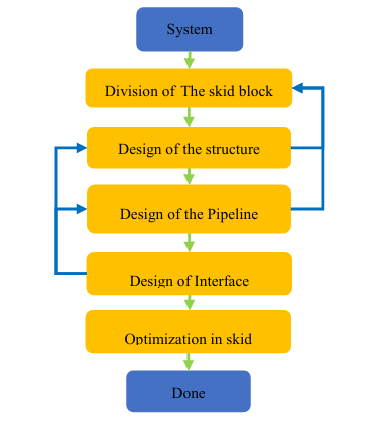
The skid block represents the smallest functional unit of the system, capable of independently performing specific process functions or even multiple functions. Within each skid block, internal components—including equipment, pipelines, wiring, instruments, and valves—are relatively independent. In principle, each medium (pipeline) within the skid block should have only one inlet and one outlet. The division of skid blocks forms the foundation for the overall skid-mounted system design. The primary objective of the division is to partition the entire process flow into distinct functional modules, each of which is structurally, logistically, and operationally independent. To initiate the division of skid blocks, the process flow must first be organized according to the overall system requirements, followed by the modularization of system functions. Based on the direction of the process flow and the mode of medium transmission, the overall planning and layout of the system's equipment should be conducted to preliminarily determine the system's form and scale. On this basis, the functions are divided to meet the following requirements:1. The functions within each skid block are relatively independent.2. The weight and dimensions of the skid block are compatible with transportation and installation constraints.3. The number of interfaces between skid blocks is minimized.
Node form |
Structure form |
Fastening method |
Positioning method |
Installation |
|
Fixed |
Butt Welding |
Welding |
None |
Complex Installation Process |
|
Detachable |
Flanged |
Flange Butt |
Bolted Connection |
Locating Pin/Bolt |
Convenient Installation |
Sleeve-type |
Sleeve Connection |
Bolted Connection |
Locating Pin/Bolt |
Convenient Installation |
|
Self-locking |
Self-locking Mechanism Connection |
Self-locking Mechanism Connection+Bolted Connection |
Locating Pin/Self-locking Positioning |
Convenient Installation |
At present, the installation structure of skid-mounted systems typically consists of a steel framework which is composed of several structural modules. Each structural module corresponds to a matching skid block to satisfy system integration requirements. Figure 2 illustrates a typical modular steel structure system, which is composed of sub-modules with similar shapes and sizes. These sub-modules are fabricated from steel and are interconnected via connecting nodes to form the complete system. The connecting nodes between sub-modules are generally classified into two types: fixed and detachable. The classification and characteristics of these nodes are summarized in Table . Fixed nodes are usually employed in systems that do not require disassembly during transportation and are predominantly connected using welding techniques. And this method is relatively mature [16]. In contrast, various detachable joints have been proposed by different researchers, including flange connections, sleeve joints, and self-locking joints. These joints typically incorporate additional fastening and positioning mechanisms to meet the structural load-bearing and disassembly requirements[17-19].
The design of the skid system structure necessitates a comprehensive approach to the segmentation of skid blocks and the spatial arrangement of the internal equipment within these blocks. Each structural module must be engineered to accommodate the specific installation requirements of individual skid blocks, ensuring that the assembled skid block adheres to the weight constraints imposed by lifting and transportation operations. The auxiliary support beams within the structural modules are strategically positioned in accordance with the equipment layout, while additional auxiliary supports are affixed to the primary beams and columns to enhance overall structural integrity.
The design of the piping layout within a chemical system must integrate multiple factors, including process requirements, operating conditions, characteristics of the conveyed materials, and the equipment layout. These measures ensure that the piping system is safe, reliable, economical, and rational, while also facilitating ease of construction, operational efficiency, and accessibility for inspection and maintenance.
In skid-mounted systems, the piping layout is modularized according to skid blocks, adhering to a primary structure of main and branch pipes. Specifically, each medium is conveyed to individual skid blocks via the main pipe, with the internal piping arrangement of each skid block conforming to relevant engineering standards and specifications.
In skid-mounted systems, interfaces can be categorized into two types: (1) the internal structure of the skid block and (2) the interfaces between skids and external skid interfaces. The internal structure of the skid block typically employs flange connections, threaded connections, welding, and other types; flange connections and welding are predominantly utilized for interfaces between skid blocks and external interfaces. The location of these interfaces is also a crucial factor in the design process. It is imperative to consider the potential impact of leaks under accidental conditions on the overall safety and functionality of the system. For instance, interfaces prone to leakage should be strategically positioned away from personnel pathways, inspection and maintenance areas, and locations of sensitive equipment.
The control system is based on a Distributed Control System (DCS) architecture. This DCS employs a hierarchical structure characterized by centralized management and decentralized control, enabling modular configuration to locally manage distinct production units. To ensure modular independence and system security, the control system topology incorporates redundancy, such that the failure of any single node does not compromise the functionality of other nodes. Functionally, the system is compartmentalized into discrete control modules, each of which can oversee one or more adjacent skids, thereby forming an integrated and self-sufficient subsystem. Correspondingly, the electrical system is designed with multiple power distribution panels, strategically positioned according to the spatial arrangement and functional demands of the skids. Each panel supplies power to one or more proximate skids.
3. Manufacturing, transportation and on-site installation of skid-mounted system
The construction of skid-mounted systems is typically divided into three primary stages: component procurement and fabrication, system integration, and system commissioning, as illustrated in Figure 3. These stages are often executed in parallel across multiple disciplines to optimize efficiency. For instance, the fabrication of equipment (such as vessels) and structural modules can proceed concurrently, while the procurement of instruments, valves, and outsourced components for the electrical and control systems can be initiated simultaneously or in advance. During the system integration phase, the assembly sequence of various components is determined by the specific construction conditions. Structural modules are usually integrated firstly. In single-skid block systems, the completion of structural module fabrication marks the establishment of construction conditions, allowing for the subsequent cross-construction and installation of equipment, instrumentation, valves, and piping. However, for multi-layer, large-scale, complex skid-mounted systems, a pre-assembly test of the structural module is typically conducted first. Based on the test results, the structural module is adjusted and integrated. Following this, equipment, instrument valves, and piping are cross-constructed and integrated according to the construction conditions. The final stage involves the installation and integration of the electrical and control systems.
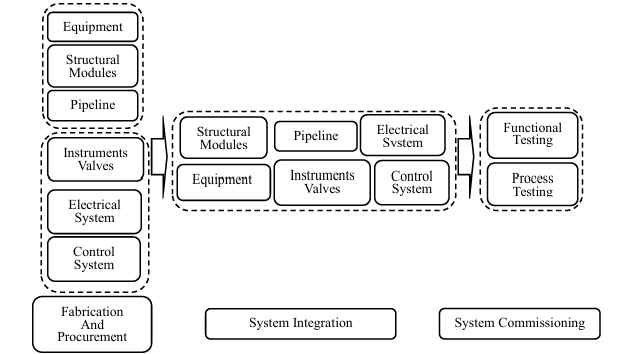
The skid-mounted system undergoes comprehensive system commissioning within the factory environment, encompassing functional validation and procedural testing. Functional validation primarily assesses the fundamental capabilities of the system's piping, electrical infrastructure, control mechanisms, and equipment, ensuring their capacity to execute essential operations. Procedural testing, in contrast, involves a holistic evaluation aligned with the standard production workflow, thereby verifying the system's proficiency in accomplishing the prescribed production sequence. Upon completion of the commissioning phase, each component of the system is primed to operate effectively under normal conditions.
The transportation of skid-mounted systems primarily involves two modes: maritime and land transportation, with the choice of mode according to the destination. For large petrochemical systems or offshore platform installations, maritime transportation is typically employed. In such cases, specialized vehicles transport the system to a port, from where it is shipped to the vicinity of the destination. Upon arrival, the system is then transported to its final location using specialized vehicles. On-site installation of the system mainly involves securing the skid in place and connecting it to external interfaces. For systems that cannot be transported by sea, the system is usually divided into road-transportable dimensions and assembled on-site. On-site assembly typically employs modular docking techniques, which significantly reduce the amount of on-site construction required.
4. Advantages and limitations of skid mounted systems
At present, the skid-mounted systems have been widely adopted across various industries in China. However, several technical challenges still remain. The integration of system skid blocks still encounters certain difficulties. For large-scale, complex skid-mounted systems involving hazardous medium, stringent safety requirements must be met. Additionally, higher mechanical performance demands are placed on the connection nodes of structural modules. Presently, detachable joints are typically connected using bolts. The large number of connecting bolts not only increases the on-site construction workload[20] but also necessitates larger joint connections to achieve the required mechanical properties[21]. In addition, significant welding deformation of the structural modules can further complicate node connections. Moreover, the residual stress induced by welding deformation imposes additional demands on the performance of connection joints.
With the development of Industry 4.0, production lines have evolved into flexible systems capable of accommodating multiple product categories and small-batch manufacturing. The inherent flexibility of skid-mounted systems aligns well with this developmental trend. However, several challenges persist. Presently, the focus of skid-mounted systems remains predominantly on in-factory integration and commissioning. These systems largely rely on empirical operations, lacking of systematic scientific guidance and mature optimization theories. Moreover, regional standards and industry-specific requirements significantly impact the standardization of skid-mounted systems.
The production of chemical products has transitioned from large-scale continuous manufacturing of single products to a mode characterized by multi-category and personalized customization. This shift necessitates flexible deployment and rapid adjustment capabilities in production lines. Currently, most skid-mounted systems are pre-assembled using structural modules as basic units, which facilitate rapid installation and deployment on-site. However, these systems often exhibit complex installation processes and limited flexibility. To meet the demands of flexible deployment and rapid adjustment, skid systems are evolving towards modularization and standardization. Skid blocks are gradually transforming into standardized modules, which serve as the smallest functional integration units. These modules can be rapidly combined to form customized production lines according to specific production requirements.
In the 21st century, environmental and energy issues have become increasingly prominent, driving a global consensus towards green, low-carbon, and sustainable development. The traditional manufacturing industry, which has long focused on mass production, has not only caused significant environmental and ecological damage but also led to substantial energy waste. In response, green and sustainable design methods—such as life cycle design for environmental performance, multi-objective optimization for remanufacturing, and design methods for green innovation—have gradually emerged. These methods prioritize environmental friendliness and aim to achieve sustainable development across multiple life cycles[22]. As a highly integrated and modular manufacturing system, the development of a full life cycle design and manufacturing approach that considers environmental performance is emerging as a key future trend.
With the advancement of technologies such as 5G communication, big data, deep learning, and edge computing, industrial intelligence has transitioned from theoretical development to practical application. As a specialized industrial manufacturing and production mode characterized by modular design and integration, the future intelligence of skid-mounted systems should encompass three key aspects: the intelligence of the design process, the digitization and intelligence of the integrated assembly process, and the intelligence of the production and operation process[23,24].Currently, the design of skid-mounted systems typically relies on designers who integrate their own experience and knowledge to synthesize and optimize the entire system. This approach, however, cannot fully address the optimization challenges inherent in the design process. With the development of artificial intelligence, various variable factors in system design can be comprehensively evaluated to obtain optimal design solutions, thereby significantly enhancing design efficiency and quality.
The pre-assembly of skid-mounted systems typically refers to the factory-based integration of components following the completion of individual manufacturing processes. This approach, while efficient, often involves substantial on-site workloads. Recent advancements in digital twin technology have enabled the establishment of complex system models, facilitating digital pre-assembly and iterative feedback loops in the design process. This integration of digital twin models significantly enhances design quality and system integration efficiency. Skid-mounted systems are widely utilized in the process industry, serving as either subsystems or integrated construction methods. With the rapid development of artificial intelligence (AI) technologies, the future of skid-mounted systems lies in achieving intelligent perception and modeling under complex working conditions, intelligent control of high-dynamic characteristics, and human-machine collaborative decision-making management. These advancements are poised to drive the next phase of innovation in skid-mounted system design and operation.
5. Conclusion
Owing to its highly integrated design, manufacturing, and installation methodologies, the skid-mounted system has rapidly gained traction in traditional process industries such as petrochemicals, basic chemicals, and fine chemicals since its inception. As technology has advanced, these systems have evolved into highly modular, integrated, and complex configurations. In this paper, we provide a concise overview of the development trajectory of skid-mounted systems. Drawing on engineering experience, we summarize the processes and key considerations associated with the design, manufacture, installation, transportation, and on-site assembly of these systems. We further analyze the current challenges and limitations of skid-mounted systems and, in conjunction with the evolution of artificial intelligence (AI) technologies, explore potential future development trends. With the ongoing progress of industrial AI, skid-mounted systems are poised to transform into complex intelligent systems characterized by highly modular intelligent perception, autonomous intelligent control, and human-machine collaborative intelligent management and decision-making, all underpinned by green design methodologies.
References
[1]. Hydrogen Leakage Location Prediction in a Fuel Cell System of Skid-Mounted Hydrogen Refueling Stations, Zhang, Leiqi ; Wu, Qiliang; Liu, Min; Chen, Hao; Wang, Dianji; Li, Xuefang; Ba, Qingxin Source: Energies, v 18, n 2, January 2025;
[2]. Design, development and performance evaluation of skid-mounted pilot wastewater treatment and resource recovery unit for mechanical scavenging vehicle; Mukherjee, Anupam (Cavitation and Dynamics Lab, Department of Process Engineering and Technology Transfer, CSIR-Indian Institute of Chemical Technology, Hyderabad; 500007, India); Chalicheemala, Srinath; Roy, Subhankar; Mullick, Aditi; De, Sirshendu; Roy, Anirban; Moulik, Siddhartha Source: Journal of Cleaner Production, v 371, October 15, 2022
[3]. Full-scale integrated skid-mounted plug flow photocatalytic reactor: Treatment of hospital wastewater; Ma, Xiaoqian; Chen, Xiaohong; Yang, Yepeng; Zhang, Chunyan; Zhang, Fabo; Chen, Daomei; Sharma, Virender K.; Wang, Jiaqiang Source: Journal of Environmental Chemical Engineering, v 12, n 1, February 2024
[4]. On-The-Fly Mixing Skid Mounted Technology Allows Cost-Effective Stimulation Jobs on Rigs with Limited Deck Space in Brazil Offshore; Carrara, M. (Baker Hughes, Rio de Janeiro, Macaé, Brazil); Colbert, F.; Gachet, R.; Garcia, F.; Pedrosa, H.; Junior, A.; Rezende, D.; deSouza, J. Source: Offshore Technology Conference Brasil, OTCB 2023, 2023, Offshore Technology Conference Brasil, OTCB 2023;
[5]. Numerical investigation on spray cooling of skid-mounted CNG air cooler under the influence of crosswind; Liu, Liansheng; Zhang, Wenrui; Li, Jifeng; Xie, Jun; Liu, Xuanchen Source: International Journal of Refrigeration, v 167, p 59-69, November 2024;
[6]. Site Trials of Methane Capture from Low-Concentration Coalbed Methane Drainage Wells Using a Mobile Skid Mounted Vacuum Pressure Swing Adsorption System. Shang, Hua (Research Institute of Special Chemicals, College of Chemistry and Chemical Engineering, Taiyuan University of Technology, Shanxi, Taiyuan; 030024, China); Bai, Honghao; Li, Xiaomin; Li, Jinping; Yang, Jiangfeng Source: SSRN, April 13, 2022
[7]. Dynamic analysis of heavy equipment mounted on steel skid foundations. Hassan, M.M. (AMEC Americas Limited, Calgary; AB, Canada); Abbas, A.; Norlander, G.W.; Bagga, J. Source: Proceedings, Annual Conference Canadian Society for Civil Engineering, v 3, p 1565-1574, 2015, Annual Conference of the Canadian Society for Civil Engineering 2014: Sustainable Municipalities
[8]. Optimizing Shale Gas Equipment Deployment Based on Pressure Distribution. Zhou, Jun (Petroleum Engineering School, Southwest Petroleum Univ., Chengdu; 610500, China); Zhou, Zonghang; Liang, Guangchuan; Li, Zichen; Hao, Baojian Source: Journal of Energy Engineering, v 150, n 6, December 1, 2024
[9]. Development and application of a skid-mounted integrated processing plant for the advanced and continuous disposal of drilling wastewater. Chen, Lirong (QHSE Surveillance and Inspection Research Institute of Chuanqing Drilling Engineering Co., Ltd., CNPC, Guanghan, Sichuan 618300, China); Li, Hui; Jiang, Xuebin; Dai, Huagao; Huang, Min; Zhang, Min Source: Natural Gas Industry, v 34, n 4, p 131-136, April 2014 Language: Chinese.
[10]. Applications of vapor recovery to crude oil production. Evans, G.B. (Hy-Bon Engineering Co., Midland; TX, United States); Nelson, Ralph Source: Society of Petroleum Engineers - SPE Automation Symposium 1968, 1968, Society of Petroleum Engineers - SPE Automation Symposium 1968.
[11]. Economical Turbine fuel production at remote locations. Burrows, M. (Pritchard Canadian Limited, Canada); Ollphant, E. Source: Annual Technical Meeting, PETSOC ATM 1967, 1967, Annual Technical Meeting, PETSOC ATM 1967.
[12]. PORTABLE PREPARATION PLANT FEATURES HEAVY MEDIA CLEANING. Mason, Richard H. Source: Coal Mining & Processing, v 13, n 11, p 56-57, Nov 1976.
[13]. A cryogenic system for processing waste gas from a PWR power generating station. Thrall, G.M. (CVI Corp., Columbus, Ohio, United States); Pilmer, D.F. Source: PROC.INST.ENVIRONM.SCI., p 144-150, 1973.
[14]. COMPLETE METERING STATIONS FOR THE OIL INDUSTRY. Anon Source: Brown Boveri Review, v 64, n 3, p 149-155, Mar 1977.
[15]. LEAK DETECTION SERVES VITAL AREA. O'Donnell, John P. Source: Oil and Gas Journal, v 70, n 30, p 33-35, Jul 24 1972
[16]. Experimental evaluation of the seismic performance of modular steel-braced frames [J]. Engineering structures, 2009, 31: 1435-1446. ANNAN C D, YOUSSEF M A, ELNAGGAR M H.
[17]. Effects of joint rotational stiffness on structural responses of multi-story modular buildings [C] The International Conference on Smart Infrastructure and Construction (ICSIC) , ICE, 2016. STYLES A J, LUO F J, BAI Y, et al.
[18]. Experimental and numerical analysis of container stack dynamics using a scaled model test [J]. Ocean engineering, 2012, 39: 24-42. SOUZA V A D, KIRKAYAK L, SUZUKI K, et al.
[19]. Behavior of C-shaped beam to square hollow section column connection in modular frame [J]. Journal of Korean society of steel construction, 2015, 27( 5) : 471-481. LEE S S, PARKKS, HONGSY, et al.
[20]. New interlocking intermodule connection for modular steel buildings: Experimental and numerical studies [J]. Engineering structures, 2019, 198: 1-15. LACEY A W, CHEN W, HAO H, et al.
[21]. Embedded steel columnto-foundation connection for a modular structural system [J]. Engineering structures, 2016, 110: 244-257. PARK K S, MOON J, LEE S S, et al.
[22]. Opportunities and Challenges of Artificial Intelligence for Green Manufacturing in the Process Industry [J]. Engineering, 2019, 995-1002, Shuai Mao, Bing Wang, Yang Tang, Feng Qian.
[23]. Intelligent Ironmaking Optimization Service on a Cloud Computing Platform by Digital Twin [J]. Engineering, (2021) 1274-1281, Heng Zhou, Chunjie Yang *, Youxian Sun
[24]. Data Analytics and Machine Learning for Smart Process Manufacturing: Recent Advances and Perspectives in the Big Data Era [J]. Engineering. (2019) 1010-1016. Chao Shang a, Fengqi You.
Cite this article
Guo,Y.;Bao,J.;Xu,Z. (2025). Development and Analysis of Skid-Mounted System. Applied and Computational Engineering,153,130-138.
Data availability
The datasets used and/or analyzed during the current study will be available from the authors upon reasonable request.
Disclaimer/Publisher's Note
The statements, opinions and data contained in all publications are solely those of the individual author(s) and contributor(s) and not of EWA Publishing and/or the editor(s). EWA Publishing and/or the editor(s) disclaim responsibility for any injury to people or property resulting from any ideas, methods, instructions or products referred to in the content.
About volume
Volume title: Proceedings of the 3rd International Conference on Mechatronics and Smart Systems
© 2024 by the author(s). Licensee EWA Publishing, Oxford, UK. This article is an open access article distributed under the terms and
conditions of the Creative Commons Attribution (CC BY) license. Authors who
publish this series agree to the following terms:
1. Authors retain copyright and grant the series right of first publication with the work simultaneously licensed under a Creative Commons
Attribution License that allows others to share the work with an acknowledgment of the work's authorship and initial publication in this
series.
2. Authors are able to enter into separate, additional contractual arrangements for the non-exclusive distribution of the series's published
version of the work (e.g., post it to an institutional repository or publish it in a book), with an acknowledgment of its initial
publication in this series.
3. Authors are permitted and encouraged to post their work online (e.g., in institutional repositories or on their website) prior to and
during the submission process, as it can lead to productive exchanges, as well as earlier and greater citation of published work (See
Open access policy for details).
References
[1]. Hydrogen Leakage Location Prediction in a Fuel Cell System of Skid-Mounted Hydrogen Refueling Stations, Zhang, Leiqi ; Wu, Qiliang; Liu, Min; Chen, Hao; Wang, Dianji; Li, Xuefang; Ba, Qingxin Source: Energies, v 18, n 2, January 2025;
[2]. Design, development and performance evaluation of skid-mounted pilot wastewater treatment and resource recovery unit for mechanical scavenging vehicle; Mukherjee, Anupam (Cavitation and Dynamics Lab, Department of Process Engineering and Technology Transfer, CSIR-Indian Institute of Chemical Technology, Hyderabad; 500007, India); Chalicheemala, Srinath; Roy, Subhankar; Mullick, Aditi; De, Sirshendu; Roy, Anirban; Moulik, Siddhartha Source: Journal of Cleaner Production, v 371, October 15, 2022
[3]. Full-scale integrated skid-mounted plug flow photocatalytic reactor: Treatment of hospital wastewater; Ma, Xiaoqian; Chen, Xiaohong; Yang, Yepeng; Zhang, Chunyan; Zhang, Fabo; Chen, Daomei; Sharma, Virender K.; Wang, Jiaqiang Source: Journal of Environmental Chemical Engineering, v 12, n 1, February 2024
[4]. On-The-Fly Mixing Skid Mounted Technology Allows Cost-Effective Stimulation Jobs on Rigs with Limited Deck Space in Brazil Offshore; Carrara, M. (Baker Hughes, Rio de Janeiro, Macaé, Brazil); Colbert, F.; Gachet, R.; Garcia, F.; Pedrosa, H.; Junior, A.; Rezende, D.; deSouza, J. Source: Offshore Technology Conference Brasil, OTCB 2023, 2023, Offshore Technology Conference Brasil, OTCB 2023;
[5]. Numerical investigation on spray cooling of skid-mounted CNG air cooler under the influence of crosswind; Liu, Liansheng; Zhang, Wenrui; Li, Jifeng; Xie, Jun; Liu, Xuanchen Source: International Journal of Refrigeration, v 167, p 59-69, November 2024;
[6]. Site Trials of Methane Capture from Low-Concentration Coalbed Methane Drainage Wells Using a Mobile Skid Mounted Vacuum Pressure Swing Adsorption System. Shang, Hua (Research Institute of Special Chemicals, College of Chemistry and Chemical Engineering, Taiyuan University of Technology, Shanxi, Taiyuan; 030024, China); Bai, Honghao; Li, Xiaomin; Li, Jinping; Yang, Jiangfeng Source: SSRN, April 13, 2022
[7]. Dynamic analysis of heavy equipment mounted on steel skid foundations. Hassan, M.M. (AMEC Americas Limited, Calgary; AB, Canada); Abbas, A.; Norlander, G.W.; Bagga, J. Source: Proceedings, Annual Conference Canadian Society for Civil Engineering, v 3, p 1565-1574, 2015, Annual Conference of the Canadian Society for Civil Engineering 2014: Sustainable Municipalities
[8]. Optimizing Shale Gas Equipment Deployment Based on Pressure Distribution. Zhou, Jun (Petroleum Engineering School, Southwest Petroleum Univ., Chengdu; 610500, China); Zhou, Zonghang; Liang, Guangchuan; Li, Zichen; Hao, Baojian Source: Journal of Energy Engineering, v 150, n 6, December 1, 2024
[9]. Development and application of a skid-mounted integrated processing plant for the advanced and continuous disposal of drilling wastewater. Chen, Lirong (QHSE Surveillance and Inspection Research Institute of Chuanqing Drilling Engineering Co., Ltd., CNPC, Guanghan, Sichuan 618300, China); Li, Hui; Jiang, Xuebin; Dai, Huagao; Huang, Min; Zhang, Min Source: Natural Gas Industry, v 34, n 4, p 131-136, April 2014 Language: Chinese.
[10]. Applications of vapor recovery to crude oil production. Evans, G.B. (Hy-Bon Engineering Co., Midland; TX, United States); Nelson, Ralph Source: Society of Petroleum Engineers - SPE Automation Symposium 1968, 1968, Society of Petroleum Engineers - SPE Automation Symposium 1968.
[11]. Economical Turbine fuel production at remote locations. Burrows, M. (Pritchard Canadian Limited, Canada); Ollphant, E. Source: Annual Technical Meeting, PETSOC ATM 1967, 1967, Annual Technical Meeting, PETSOC ATM 1967.
[12]. PORTABLE PREPARATION PLANT FEATURES HEAVY MEDIA CLEANING. Mason, Richard H. Source: Coal Mining & Processing, v 13, n 11, p 56-57, Nov 1976.
[13]. A cryogenic system for processing waste gas from a PWR power generating station. Thrall, G.M. (CVI Corp., Columbus, Ohio, United States); Pilmer, D.F. Source: PROC.INST.ENVIRONM.SCI., p 144-150, 1973.
[14]. COMPLETE METERING STATIONS FOR THE OIL INDUSTRY. Anon Source: Brown Boveri Review, v 64, n 3, p 149-155, Mar 1977.
[15]. LEAK DETECTION SERVES VITAL AREA. O'Donnell, John P. Source: Oil and Gas Journal, v 70, n 30, p 33-35, Jul 24 1972
[16]. Experimental evaluation of the seismic performance of modular steel-braced frames [J]. Engineering structures, 2009, 31: 1435-1446. ANNAN C D, YOUSSEF M A, ELNAGGAR M H.
[17]. Effects of joint rotational stiffness on structural responses of multi-story modular buildings [C] The International Conference on Smart Infrastructure and Construction (ICSIC) , ICE, 2016. STYLES A J, LUO F J, BAI Y, et al.
[18]. Experimental and numerical analysis of container stack dynamics using a scaled model test [J]. Ocean engineering, 2012, 39: 24-42. SOUZA V A D, KIRKAYAK L, SUZUKI K, et al.
[19]. Behavior of C-shaped beam to square hollow section column connection in modular frame [J]. Journal of Korean society of steel construction, 2015, 27( 5) : 471-481. LEE S S, PARKKS, HONGSY, et al.
[20]. New interlocking intermodule connection for modular steel buildings: Experimental and numerical studies [J]. Engineering structures, 2019, 198: 1-15. LACEY A W, CHEN W, HAO H, et al.
[21]. Embedded steel columnto-foundation connection for a modular structural system [J]. Engineering structures, 2016, 110: 244-257. PARK K S, MOON J, LEE S S, et al.
[22]. Opportunities and Challenges of Artificial Intelligence for Green Manufacturing in the Process Industry [J]. Engineering, 2019, 995-1002, Shuai Mao, Bing Wang, Yang Tang, Feng Qian.
[23]. Intelligent Ironmaking Optimization Service on a Cloud Computing Platform by Digital Twin [J]. Engineering, (2021) 1274-1281, Heng Zhou, Chunjie Yang *, Youxian Sun
[24]. Data Analytics and Machine Learning for Smart Process Manufacturing: Recent Advances and Perspectives in the Big Data Era [J]. Engineering. (2019) 1010-1016. Chao Shang a, Fengqi You.