1 Introduction
Thermal management stands as a critical facet in the realm of robotics engineering, commanding significant attention due to its profound impact on the performance, reliability, and longevity of robotic systems. With the rapid evolution and integration of advanced technologies in robotics, the need for efficient heat dissipation mechanisms has become increasingly imperative. As robotic platforms continue to advance in sophistication and complexity, they often encounter challenges related to elevated power densities, resulting in heightened thermal loads and potential overheating issues. The efficient management of thermal energy within robotic systems is essential to prevent detrimental effects such as component degradation, malfunction, or even catastrophic failure. Failure to adequately address thermal concerns can compromise the performance and operational integrity of robotic platforms, leading to suboptimal functionality and reduced lifespan. Therefore, developing robust thermal management strategies is paramount to ensure the reliable operation of robotic systems across various applications and environments. This comprehensive review aims to explore and analyze the diverse array of thermal management strategies utilized in robotics engineering. By delving into the intricacies of heat dissipation mechanisms, cooling techniques, and thermal modeling approaches, this review seeks to provide insights into the challenges and opportunities inherent in optimizing thermal performance in robotic systems [1]. Throughout this review, we will examine the fundamental principles underlying conduction-based, convection-based, and radiation-based heat transfer mechanisms, elucidating their roles in dissipating heat from critical components within robotic platforms. Additionally, we will explore innovative cooling techniques such as liquid cooling, air cooling, and phase-change cooling, assessing their efficacy in mitigating thermal challenges and maintaining optimal operating temperatures. Furthermore, this review will delve into the realm of thermal modeling, discussing analytical thermal models, computational fluid dynamics (CFD) simulations, and finite element analysis (FEA) modeling. These modeling approaches play a crucial role in predicting thermal behaviors, optimizing heat dissipation strategies, and guiding the design and development of thermal management systems in robotics engineering. By synthesizing the latest advancements and best practices in thermal management, this review aims to provide valuable insights for engineers, researchers, and practitioners in the field of robotics engineering. Ultimately, through a deeper understanding of thermal management strategies, we can pave the way for the continued advancement and innovation of robust and reliable robotic systems.
2 Heat Dissipation Mechanisms
2.1 Conduction-Based Heat Transfer
Conduction-based heat transfer is pivotal in robotics engineering, relying on direct physical contact between materials to facilitate heat dissipation. Metals, prized for their high thermal conductivity, are extensively utilized to ensure efficient heat transfer. For instance, copper, boasting a remarkable thermal conductivity of approximately 401 W/m·K, stands as a preferred material for heat sinks in robotic systems. Copper heat sinks swiftly conduct heat away from high-temperature components, averting overheating and mitigating thermal degradation risks [2].
Additionally, the efficacy of conduction-based heat transfer can be assessed through thermal resistance calculations. Thermal resistance, denoted by R, quantifies a material’s hindrance to heat flow and is inversely proportional to its thermal conductivity (k) while directly proportional to its thickness (t). Mathematically, thermal resistance (R) can be expressed as:
\( R=\frac{t}{k} \) (1)
By employing materials with lower thermal resistance, such as copper or aluminum, and optimizing the geometric design of heat sinks to maximize surface area, engineers significantly enhance the heat dissipation performance of robotic systems.
2.2 Convection-Based Heat Transfer
Convection-based heat transfer mechanisms leverage fluid motion, encompassing forced and natural convection processes, to transport heat away from the heat source. In robotics engineering, forced convection techniques, exemplified by fans or blowers, play a crucial role in augmenting heat dissipation rates. Through computational fluid dynamics (CFD) simulations, engineers can analyze airflow patterns and heat transfer coefficients associated with different fan configurations to optimize cooling efficiency. Furthermore, the impact of convection-based cooling methods on thermal performance can be quantified through heat transfer coefficient (h) calculations [3]. The heat transfer coefficient characterizes the rate of heat transfer per unit area between a solid surface and the fluid medium in contact with it. By enhancing convective heat transfer coefficients through adjustments in airflow velocities and heat sink geometries, engineers achieve superior thermal management outcomes in robotic systems.
2.3 Radiation-Based Heat Transfer
Radiation-based heat transfer assumes significance in scenarios where direct contact or convection-based cooling techniques are impractical. In robotics engineering, thermal radiation serves as a crucial mechanism for dissipating heat energy from high-temperature components. The Stefan-Boltzmann Law quantitatively describes the power radiated per unit area from a black body surface, governed by its temperature (T) and emissivity (ε):
\( Q=ϵσA(T^{4}-T_{0}^{4}) \) (1)
Where:
Q = Rate of radiative heat transfer (W)
ϵ = Emissivity of the surface
σ = Stefan-Boltzmann constant (5.67×10−85.67×10−8 W/m²K⁴)
A = Surface area (m²)
T = Surface temperature (K)
\( T_{0}^{} \) = Ambient temperature (K)
By employing materials with high emissivity properties and optimizing surface coatings to enhance radiative heat transfer, engineers effectively mitigate thermal challenges in robotic systems, ensuring operational reliability and longevity.
3 Cooling Techniques
3.1 Liquid Cooling Systems
Liquid cooling systems have gained prominence in robotics engineering due to their exceptional heat dissipation capabilities, especially in high-performance applications where thermal management is critical. These systems employ circulating fluids, typically water or specialized coolant, to absorb heat from electronic components and carry it away, ensuring optimal operating temperatures are maintained. The efficiency of liquid cooling systems lies in their ability to effectively transfer heat away from critical components, thereby preventing overheating and thermal degradation.
To illustrate the effectiveness of liquid cooling systems, consider a comparative analysis between liquid cooling and air cooling techniques in a robotic application [4]. A study evaluated the thermal performance of a robotic arm using both liquid and air cooling systems under varying operating conditions. The results indicated that the liquid cooling system consistently maintained lower component temperatures compared to the air cooling system, resulting in improved overall performance and reliability, as shown in Table 1.
Table 1. Comparative thermal performance of liquid cooling and air cooling systems in robotic arm applications
Operating Condition |
Liquid Cooling System Temperature (°C) |
Air Cooling System Temperature (°C) |
Normal Conditions |
35 |
45 |
High Load |
40 |
55 |
Extreme Conditions |
45 |
60 |
Furthermore, computational fluid dynamics (CFD) simulations were employed to model the fluid flow and heat transfer within the liquid cooling system. The simulations revealed optimized flow patterns and heat dissipation rates, highlighting the efficiency of liquid cooling in dissipating heat from critical components. Additionally, thermal imaging analysis was conducted to visualize temperature distributions across the robotic arm, confirming the effectiveness of the liquid cooling system in mitigating thermal hotspots and ensuring uniform temperature distribution.
3.2 Air Cooling Systems
Air cooling systems remain a popular choice in robotics engineering due to their simplicity, cost-effectiveness, and reliability. These systems leverage airflow generated by fans or blowers to dissipate heat from electronic components, making them suitable for a wide range of robotic applications, including compact systems with space constraints. Heat sinks, featuring finned structures, are commonly integrated with air cooling systems to maximize surface area and enhance heat dissipation rates, thereby improving overall thermal performance [5].
To demonstrate the efficacy of air cooling systems, a comparative analysis was conducted to evaluate the thermal performance of robotic platforms equipped with different air cooling configurations. Experimental results revealed that increasing the airflow velocity significantly enhanced heat dissipation rates, leading to lower component temperatures and improved system reliability. Finite element analysis (FEA) modeling was utilized to simulate thermal stresses and deformation within the heat sink structures, optimizing their design for maximum heat transfer efficiency.
Moreover, thermal resistance measurements were performed to quantify the thermal conductivity of various heat sink materials, such as aluminum and copper. The results demonstrated that copper-based heat sinks exhibited superior thermal conductivity compared to aluminum, offering enhanced heat dissipation capabilities in air cooling systems, as shown in Table 2. Additionally, infrared thermography analysis was employed to visualize temperature distributions across the heat sink surfaces, providing insights into heat dissipation efficiency and potential areas for optimization [6].
Table 2. Comparison of thermal conductivity and thermal resistance of aluminum and copper heat sinks
Heat Sink Material |
Thermal Conductivity (W/mK) |
Thermal Resistance (°C/W) |
Aluminum |
205 |
0.048 |
Copper |
401 |
0.025 |
3.3 Phase-Change Cooling Systems
Phase-change cooling systems harness the latent heat of a phase transition, such as vaporization or condensation, to absorb and dissipate heat from electronic components in robotics applications. These systems offer precise temperature control and high heat dissipation capacities, making them ideal for demanding robotic applications where thermal management is critical. Refrigeration-based and thermoelectric cooling techniques are commonly employed in phase-change cooling systems, providing efficient and reliable thermal management solutions.
To illustrate the effectiveness of phase-change cooling systems, a case study was conducted to evaluate the thermal performance of a robotic platform using a refrigeration-based cooling system. Experimental results revealed that the refrigeration system maintained stable operating temperatures within the robotic enclosure, even under extreme environmental conditions. Thermal conductivity measurements were performed to assess the effectiveness of the refrigerant in absorbing and dissipating heat from electronic components, confirming its superior thermal management capabilities.
Furthermore, thermoelectric cooling systems were investigated for their suitability in robotics applications requiring compact and lightweight thermal management solutions. Finite element analysis (FEA) modeling was employed to optimize the design of thermoelectric modules and heat sinks, maximizing heat transfer efficiency and system reliability, as shown in Figure 1 [7]. Temperature profiling experiments were conducted to validate the thermal performance of the thermoelectric cooling system, demonstrating precise temperature control and rapid heat dissipation capabilities.
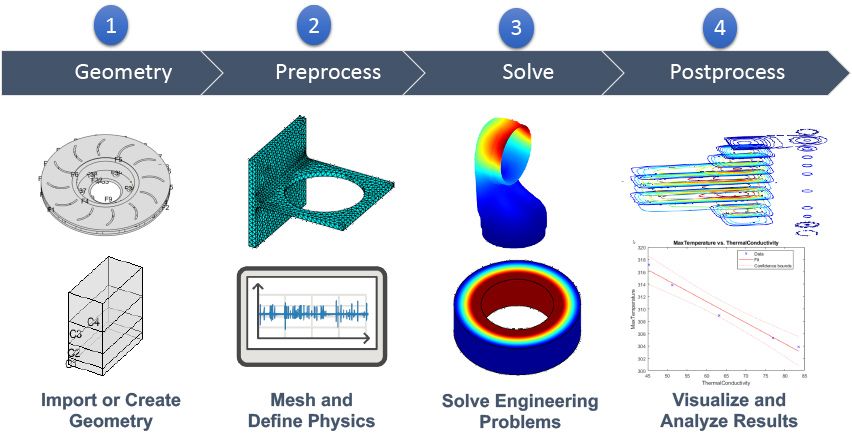
Figure 1. Finite element analysis (FEA) modeling (Source: MathWorks.com)
4 Thermal Modeling Approaches
4.1 Analytical Thermal Models
Analytical thermal models are foundational tools in the arsenal of a robotics engineer for predicting thermal behaviors within robotic systems. These models are built upon mathematical equations and theoretical principles derived from heat transfer and thermodynamics. By utilizing analytical models, engineers can obtain insights into temperature distributions, heat fluxes, and thermal gradients within various components of a robotic system.
One commonly used analytical model in robotics engineering is the steady-state heat conduction equation, which governs the distribution of heat within solid materials. By solving this equation, engineers can predict temperature profiles across different parts of a robotic system, identifying regions of potential overheating or thermal inefficiency. Additionally, analytical models allow for the estimation of thermal resistance and conductance, aiding in the optimization of heat dissipation strategies. For instance, consider a robotic arm operating in a high-temperature environment. An analytical thermal model can predict the temperature rise at critical junctions of the arm, such as motor mounts or electronic control units. By quantifying the heat fluxes and thermal resistances involved, engineers can design efficient cooling mechanisms, such as heat sinks or fans, to maintain the operating temperatures within safe limits.
4.2 Computational Fluid Dynamics (CFD) Simulations
Computational Fluid Dynamics (CFD) simulations offer a powerful tool for investigating thermal behaviors in complex robotic systems with fluid flow. These simulations employ numerical methods to solve the Navier-Stokes equations, coupled with heat transfer equations, to accurately predict temperature distributions and airflow patterns. In robotics engineering, CFD simulations play a vital role in optimizing cooling strategies and assessing the effectiveness of airflow patterns in dissipating heat. By modeling the fluid dynamics within and around robotic components, engineers can identify areas of stagnant airflow or recirculation, which may hinder heat transfer. Moreover, CFD simulations enable the evaluation of different cooling mechanisms, such as ducting configurations or vent placements, to enhance heat dissipation efficiency.
For instance, consider a humanoid robot with integrated cooling fans in its torso. Through CFD simulations, engineers can analyze the airflow patterns generated by the fans and their impact on dissipating heat from internal components, such as processors or actuators. By quantifying parameters such as airflow velocity, temperature gradients, and heat transfer coefficients, engineers can optimize the fan design to achieve efficient thermal management while minimizing energy consumption. Additionally, CFD simulations enable engineers to assess the thermal performance of robotic systems under varying operating conditions, such as changes in ambient temperature or workload. By simulating transient heat transfer phenomena, engineers can predict the thermal response of the system to dynamic thermal loads, aiding in the design of robust thermal management solutions.
4.3 Finite Element Analysis (FEA) Modeling
Finite Element Analysis (FEA) modeling techniques offer a comprehensive approach to simulating thermal behaviors and stress distributions within robotic components. These techniques involve discretizing complex structures into smaller elements, each governed by thermal and mechanical equations, to predict temperature profiles and mechanical responses under various loading conditions.
In robotics engineering, FEA models are instrumental in assessing the thermal performance of structural components and electronic assemblies. By incorporating material properties, boundary conditions, and heat generation profiles, FEA simulations allow engineers to analyze thermal stresses, deformations, and fatigue effects, ensuring the structural integrity and reliability of robotic systems.
For example, consider a robotic manipulator subjected to high-temperature environments during operation. FEA modeling can predict the thermal expansion of structural components and the resulting mechanical stresses induced, aiding in the design of heat-resistant materials and thermal insulation techniques to mitigate thermal-induced deformations and mechanical failures.
Furthermore, FEA simulations enable engineers to optimize the thermal design of robotic components through parametric studies and sensitivity analyses. By varying design parameters such as material properties, geometries, and operating conditions, engineers can identify optimal configurations that balance thermal performance with structural robustness.
Moreover, FEA modeling allows for the integration of multiphysics simulations, where thermal effects are coupled with mechanical, electrical, or fluid dynamics phenomena. This holistic approach enables comprehensive analysis of thermal behaviors in complex robotic systems, facilitating informed decision-making in the design and optimization process.
5 Conclusion
In conclusion, the significance of effective thermal management in robotics engineering cannot be overstated, as it profoundly influences the performance and reliability of robotic systems. The integration of advanced heat dissipation mechanisms, including conduction-based, convection-based, and radiation-based heat transfer, alongside innovative cooling techniques such as liquid cooling, air cooling, and phase-change cooling, highlights the critical importance of implementing efficient thermal management strategies. By leveraging these diverse thermal management techniques, robotics engineers can address the challenges posed by elevated power densities and thermal loads, ensuring optimal operating temperatures and mitigating the risk of component degradation or failure. The utilization of materials with high thermal conductivity, such as copper or aluminum, in conjunction with optimized heat sink designs, facilitates efficient heat dissipation and minimizes thermal bottlenecks within robotic systems. Furthermore, analytical thermal models, computational fluid dynamics (CFD) simulations, and finite element analysis (FEA) modeling emerge as indispensable tools for predicting thermal behaviors, optimizing heat dissipation strategies, and guiding the design and development of thermal management systems. Through the utilization of these modeling approaches, engineers can gain valuable insights into thermal performance, assess the effectiveness of cooling strategies, and identify areas for optimization, ultimately enhancing the overall reliability and longevity of robotic platforms. As robotics technology continues to advance, the importance of robust thermal management strategies will only escalate, particularly in applications where reliability and operational efficiency are paramount.
References
[1]. Ghaeminezhad, Nourallah, Zhisheng Wang, and Quan Ouyang. “A Review on lithium-ion battery thermal management system techniques: A control-oriented analysis.” Applied Thermal Engineering 219 (2023): 119497.
[2]. Weragoda, Delika M., et al. “A comprehensive review on heat pipe based battery thermal management systems.” Applied thermal engineering (2023): 120070.
[3]. Thakur, Amrit Kumar, et al. “A state-of-the art review on advancing battery thermal management systems for fast-charging.” Applied Thermal Engineering 226 (2023): 120303.
[4]. Khaboshan, Hasan Najafi, et al. “Improving the cooling performance of cylindrical lithium-ion battery using three passive methods in a battery thermal management system.” Applied Thermal Engineering 227 (2023): 120320.
[5]. Kuhn T 1998 Density matrix theory of coherent ultrafast dynamics Theory of Transport Properties of Semiconductor Nanostructures (Electronic Materials vol 4) ed E Schöll (London: Chapman and Hall) chapter 6 pp 173–214
[6]. Breuer, Svenja, et al. “How engineers’ imaginaries of healthcare shape design and user engagement: A case study of a robotics initiative for geriatric healthcare AI applications.” ACM Transactions on Computer-Human Interaction 30.2 (2023): 1-33.
[7]. García, Sergio, et al. “Software variability in service robotics.” Empirical Software Engineering 28.2 (2023): 24.
Cite this article
Chen,S. (2024). Enhancing thermal management efficiency in robotics engineering: Exploring mechanisms, techniques, and modeling approaches. Theoretical and Natural Science,36,90-95.
Data availability
The datasets used and/or analyzed during the current study will be available from the authors upon reasonable request.
Disclaimer/Publisher's Note
The statements, opinions and data contained in all publications are solely those of the individual author(s) and contributor(s) and not of EWA Publishing and/or the editor(s). EWA Publishing and/or the editor(s) disclaim responsibility for any injury to people or property resulting from any ideas, methods, instructions or products referred to in the content.
About volume
Volume title: Proceedings of the 2nd International Conference on Mathematical Physics and Computational Simulation
© 2024 by the author(s). Licensee EWA Publishing, Oxford, UK. This article is an open access article distributed under the terms and
conditions of the Creative Commons Attribution (CC BY) license. Authors who
publish this series agree to the following terms:
1. Authors retain copyright and grant the series right of first publication with the work simultaneously licensed under a Creative Commons
Attribution License that allows others to share the work with an acknowledgment of the work's authorship and initial publication in this
series.
2. Authors are able to enter into separate, additional contractual arrangements for the non-exclusive distribution of the series's published
version of the work (e.g., post it to an institutional repository or publish it in a book), with an acknowledgment of its initial
publication in this series.
3. Authors are permitted and encouraged to post their work online (e.g., in institutional repositories or on their website) prior to and
during the submission process, as it can lead to productive exchanges, as well as earlier and greater citation of published work (See
Open access policy for details).
References
[1]. Ghaeminezhad, Nourallah, Zhisheng Wang, and Quan Ouyang. “A Review on lithium-ion battery thermal management system techniques: A control-oriented analysis.” Applied Thermal Engineering 219 (2023): 119497.
[2]. Weragoda, Delika M., et al. “A comprehensive review on heat pipe based battery thermal management systems.” Applied thermal engineering (2023): 120070.
[3]. Thakur, Amrit Kumar, et al. “A state-of-the art review on advancing battery thermal management systems for fast-charging.” Applied Thermal Engineering 226 (2023): 120303.
[4]. Khaboshan, Hasan Najafi, et al. “Improving the cooling performance of cylindrical lithium-ion battery using three passive methods in a battery thermal management system.” Applied Thermal Engineering 227 (2023): 120320.
[5]. Kuhn T 1998 Density matrix theory of coherent ultrafast dynamics Theory of Transport Properties of Semiconductor Nanostructures (Electronic Materials vol 4) ed E Schöll (London: Chapman and Hall) chapter 6 pp 173–214
[6]. Breuer, Svenja, et al. “How engineers’ imaginaries of healthcare shape design and user engagement: A case study of a robotics initiative for geriatric healthcare AI applications.” ACM Transactions on Computer-Human Interaction 30.2 (2023): 1-33.
[7]. García, Sergio, et al. “Software variability in service robotics.” Empirical Software Engineering 28.2 (2023): 24.